Power loss in farming machinery, especially in tractors, can have far-reaching effects on agricultural productivity. As modern farming becomes increasingly reliant on complex machinery for efficiency, power loss due to mechanical failure can result in delays in the field, increased fuel consumption, and reduced overall operational efficiency. In a world where timing and cost-effectiveness are critical, even a small dip in tractor power can lead to extended downtime and a significant loss in revenue.
Farmers and equipment managers are often left wondering, “Why is my tractor losing power so frequently?” Understanding the root causes behind these power issues is the first step in addressing them. Common failures such as clogged filters, worn-out components, and hydraulic problems are often the main culprits, but there are other less obvious causes too. Is there a way to prevent such frequent power losses? Yes, a comprehensive and strategic maintenance plan can dramatically reduce the frequency of these failures and help optimize machine performance.
This article will delve into the causes of power loss in tractors, explain how to diagnose the issue, and offer effective solutions for minimizing such disruptions. We’ll explore various preventative maintenance techniques and technological advancements that can not only restore but improve tractor performance. Stay tuned for practical tips on keeping your equipment running efficiently, so you can focus more on the farm and less on repairs.
Contents
- 1 1. Diagnostic Basics: Signs Your Tractor Is Losing Power
- 2 2. Core Mechanical Failures Behind Power Loss
- 3 3. Preventive Maintenance: How to Minimize Power Loss
- 4 4. When to Replace vs. When to Repair: Decision Guide
- 5 5. Case Studies: Solving Power Loss for Farmers Worldwide
- 6 Conclusion: Power Loss Is Preventable
1. Diagnostic Basics: Signs Your Tractor Is Losing Power
When a tractor starts to lose power, it can manifest in different ways. Often, these signs appear subtly at first, making it difficult for operators to immediately recognize the root causes. However, understanding these symptoms early on can save you from costly repairs and prolonged downtime. Here’s a more in-depth look at the most common signs that your tractor may be losing power, along with explanations of what they mean and potential solutions.
1.1 Reduced Acceleration and Unusual Engine Sounds
Symptoms:
When you try to accelerate the tractor, the response is slower than usual, or the engine hesitates to pick up speed.
Strange noises like knocking or pinging sounds coming from the engine, which can indicate misfires or inefficiency in combustion.
Causes:
Clogged fuel filters: Reduced fuel flow leads to a poor air-fuel mixture, resulting in sluggish acceleration and engine strain.
Fuel injectors malfunctioning: If injectors aren’t delivering the correct amount of fuel to the cylinders, it can cause delayed combustion and loss of power.
Air intake issues: A dirty or blocked air filter can also prevent proper airflow to the engine, leading to slower acceleration and engine stuttering.
Solution:
Regular filter checks: Clean or replace the air and fuel filters regularly to ensure smooth airflow and fuel delivery.
Injector maintenance: Have your injectors cleaned or replaced if they are not functioning optimally.
1.2 Lower Working Efficiency and Decreased Load Handling
Symptoms:
Tractor struggles to pull heavy loads or run attachments at full capacity.
You may notice that the tractor’s power output decreases while working, and the engine seems to overheat or stall under load.
Causes:
Hydraulic system failure: The hydraulic system is often responsible for powering equipment attached to the tractor. If there’s a loss in hydraulic pressure or a leak, the tractor will struggle to maintain power and efficiency.
Transmission problems: If the transmission is worn or malfunctioning, power transfer from the engine to the wheels becomes inefficient, resulting in a loss of effective power.
Clutch wear: An aging or worn-out clutch plate may slip, causing inefficient power transfer, especially under load.
Solution:
Hydraulic system inspection: Regularly inspect hydraulic hoses and fluid levels to ensure efficient operation.
Clutch checks: Make sure that the clutch and transmission are regularly maintained to avoid unnecessary power losses under load.
1.3 Increased Fuel Consumption Without Increased Workload
Symptoms:
If the tractor is burning more fuel than usual, but you’re not using it for heavier tasks, this could be a significant sign of power loss.
Your fuel gauge seems to drop rapidly, and there’s no noticeable increase in workload.
Causes:
Inefficient combustion: A clogged air filter or malfunctioning fuel system can cause the engine to burn more fuel than necessary, especially if the combustion process is inefficient.
Excessive idling: Tractor idling for extended periods without being properly maintained could lead to fuel wastage, as the engine is not working at optimal capacity.
Low tire pressure: Low tire pressure increases rolling resistance, requiring the engine to work harder and consume more fuel.
Solution:
Fuel system maintenance: Ensure regular servicing of the fuel system, including checking the fuel injectors, fuel pump, and filters.
Tire pressure checks: Regularly check tire pressure and ensure they are properly inflated to reduce rolling resistance and improve fuel efficiency.
1.4 Abnormal Engine Temperature or Overheating
Symptoms:
If the engine temperature seems to rise rapidly, or if the temperature gauge shows high readings, it’s a clear indication that the tractor isn’t functioning as it should.
In some cases, engine power may decrease as the tractor attempts to prevent overheating.
Causes:
Cooling system failure: A leak in the radiator, clogged coolant channels, or a malfunctioning water pump can all lead to inadequate cooling, causing the engine to overheat.
Dirty radiator or air intakes: Dirt or debris can block airflow to the radiator, reducing the system’s cooling capacity and causing engine strain.
Solution:
Coolant checks: Ensure the coolant levels are optimal and check for leaks or blockages in the radiator and cooling system.
Airflow clearance: Regularly clean the radiator and ensure that air passages are free of debris to promote better cooling.
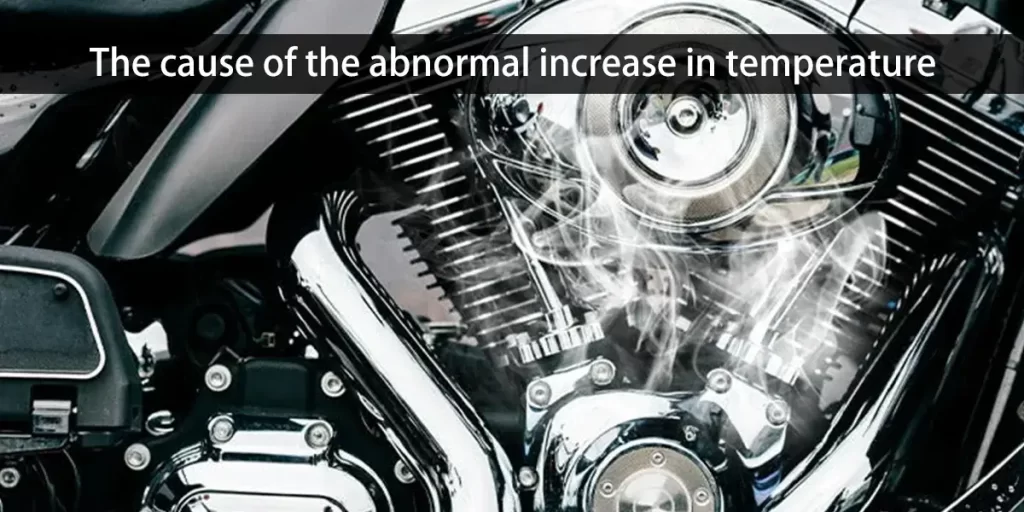
2. Core Mechanical Failures Behind Power Loss
When a tractor loses power, it’s often due to mechanical failures within the system that gradually hinder its performance. Identifying these failures early on can prevent further damage, avoid unexpected downtime, and improve long-term efficiency. In this section, we’ll dive into the most common mechanical failures that lead to power loss in tractors and provide actionable solutions to mitigate them.
2.1 Fuel System Issues
Signs of Failure:
Inconsistent engine power, irregular acceleration, or the engine stalling under load.
A noticeable decrease in engine response, particularly during startup or under load conditions.
Causes:
Clogged fuel filter: Over time, dirt and debris can clog the fuel filter, restricting fuel flow and causing inefficient combustion.
Fuel pump failure: A malfunctioning fuel pump may fail to supply the engine with enough fuel, leading to power loss.
Injector problems: Faulty or dirty injectors can lead to uneven fuel distribution, resulting in poor engine performance.
Solution:
Regular fuel system checks: Inspect the fuel pump and injectors regularly and replace filters as per the manufacturer’s guidelines.
Use high-quality fuel: Ensure clean, filtered fuel is used to reduce the chances of clogging and contaminating the system.
2.2 Air Intake and Filtration Problems
Signs of Failure:
Loss of engine power during acceleration.
Excessive black smoke from the exhaust or abnormal engine sounds.
Causes:
Clogged air filter: In environments with dust, debris, or pollen, the air filter can become clogged quickly, restricting airflow to the engine. This leads to inefficient combustion, reduced engine performance, and increased fuel consumption.
Intake system leakage: Cracks or loose connections in the intake system can allow unfiltered air into the engine, which may result in damage to internal components over time.
Solution:
Regular air filter checks: Replace or clean the air filter every 100–150 hours of use, or more frequently in dusty conditions.
Inspect intake system: Ensure there are no leaks in the intake manifold or air ducts that could compromise air quality.
2.3 Exhaust and Emissions Blockage
Signs of Failure:
Decreased power and increased fuel consumption.
Engine stuttering, erratic performance, or failure to reach optimal RPM.
Causes:
DPF (Diesel Particulate Filter) clogging: A clogged DPF can prevent exhaust gases from exiting properly, causing increased backpressure and reducing engine power.
Exhaust system obstruction: A blocked exhaust or failing EGR (Exhaust Gas Recirculation) valve can hinder engine exhaust flow, leading to poor combustion efficiency.
Solution:
Regular DPF regeneration: Perform regular cleaning or regeneration of the DPF as per the manufacturer’s instructions to maintain optimal exhaust flow.
Exhaust system inspection: Ensure there are no blockages in the exhaust pipes or issues with the EGR valve that could restrict exhaust flow.
2.4 Engine Wear and Compression Loss
Signs of Failure:
Difficulty starting the engine, or rough idling.
Decreased engine power, especially under load, and increased fuel consumption.
Causes:
Cylinder wear: Over time, wear and tear on engine cylinders can result in lower compression, leading to inefficient engine performance.
Piston ring failure: Worn or broken piston rings allow combustion gases to escape, reducing the engine’s power and efficiency.
Solution:
Compression tests: Regularly check the engine’s compression levels to ensure it’s within the manufacturer’s specifications.
Engine rebuild or overhaul: If compression loss is significant, consider overhauling the engine or replacing damaged components such as pistons, rings, and valves.
2.5 Transmission and Clutch Malfunction
Signs of Failure:
Slipping gears, difficulty shifting, or unexpected stalling during gear changes.
Loss of power transmission or reduced efficiency in transferring power from the engine to the wheels.
Causes:
Clutch plate wear: Prolonged use of the clutch, especially under heavy loads, can lead to slipping or overheating, reducing power transmission efficiency.
Transmission fluid issues: Low or contaminated transmission fluid can cause poor gear shifting, or even lead to internal damage in the gearbox.
Solution:
Clutch maintenance: Regularly inspect the clutch for wear and ensure proper adjustment to avoid slippage or excessive strain.
Transmission fluid checks: Keep an eye on fluid levels and replace them as needed. Ensure that only the recommended fluid is used to prevent clogs or system failure.
2.6 Hydraulic System Overload
Signs of Failure:
Loss of power while operating attachments or hydraulic implements.
The tractor struggles with lifting or controlling implements, or the hydraulic system is noisy or unresponsive.
Causes:
Overworked hydraulic system: Frequent use of heavy equipment or overloading the hydraulic system can cause overheating or strain on the pump, leading to power loss.
Leaks or air in the system: Leaks or air contamination in the hydraulic lines can reduce pressure, making the system less efficient.
Solution:
Hydraulic system inspection: Check for leaks or signs of damage in the hydraulic lines and seals.
System maintenance: Regularly replace hydraulic fluid and perform a fluid change when necessary to prevent system failure.
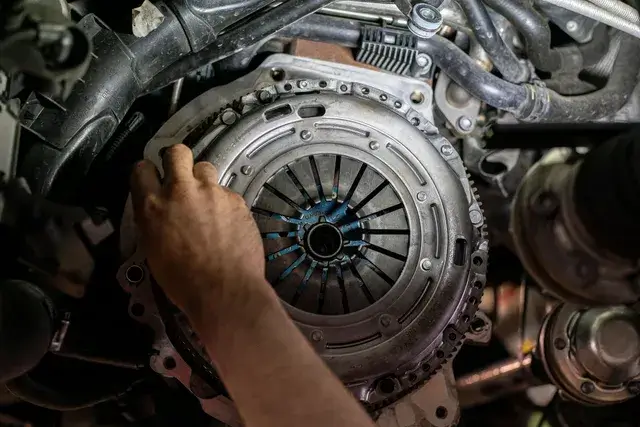
3. Preventive Maintenance: How to Minimize Power Loss
Preventive maintenance is crucial in ensuring that your tractor operates efficiently and continues to deliver optimal performance. By regularly checking and maintaining key systems, you can significantly reduce power loss, avoid costly repairs, and extend the lifespan of your equipment. Here are some essential preventive measures to minimize power loss and keep your tractor in top condition.
3.1 Regularly Replace Fuel Filters and Maintain the Fuel System
Fuel filters play a critical role in maintaining engine performance by ensuring that only clean fuel enters the system. A clogged or dirty filter can cause fuel flow issues, leading to power loss and engine inefficiency.
Action Plan:
Replace the fuel filter regularly: Depending on your operational conditions, replace the fuel filter every 200–300 hours of operation. More frequent replacements may be necessary for tractors operating in dusty environments.
Inspect fuel lines: Look for cracks, leaks, or damage to the fuel lines that could lead to power loss.
Maintain fuel injectors: Clean or replace the fuel injectors if they become clogged or worn out, as this can significantly impact engine performance.
Impact: Regular maintenance of the fuel system ensures smooth fuel delivery, preventing power loss and extending the life of the engine.
3.2 Clean or Replace Air Filters Regularly
The air filter is essential in ensuring that only clean air enters the engine. A clogged air filter restricts airflow, reducing the amount of oxygen available for combustion and causing the engine to lose power.
Action Plan:
Inspect the air filter every 100 hours of operation: In dusty or harsh conditions, clean or replace the air filter more frequently.
Clean the filter properly: Use compressed air to clean the filter (do not exceed 0.2 MPa pressure) or wash it if required. Ensure that no debris remains before reinstalling.
Use a high-quality filter: Invest in a high-efficiency air filter to ensure optimal filtration, especially in environments with high dust levels.
Impact: A clean air filter helps the engine “breathe” easily, improving fuel efficiency and reducing unnecessary power loss.
3.3 Inspect and Maintain the Fuel Injection System
The fuel injection system controls how fuel is delivered to the engine. If the injectors or sensors are not functioning properly, it can lead to poor fuel combustion, resulting in power loss and inefficient engine performance.
Action Plan:
Check injectors: Perform regular checks to ensure the injectors are clean and functioning correctly. If necessary, clean them using a specialized injector cleaning solution.
Monitor sensor performance: Ensure that sensors such as the mass airflow sensor and oxygen sensor are calibrated correctly and functioning within specifications.
Check for leaks: Inspect the fuel lines and injectors for any signs of leaks that could cause fuel inefficiency.
Impact: A well-maintained fuel injection system ensures precise fuel delivery, resulting in better combustion and reduced power loss.
3.4 Utilize MINNUO’s Remote Diagnostic System for Early Detection
Technological advancements, like remote diagnostics, can significantly enhance preventive maintenance efforts. MINNUO’s remote diagnostic system can track tractor performance in real-time and notify you of any irregularities, allowing for early intervention before power loss becomes a major issue.
Action Plan:
Set up remote monitoring: Integrate MINNUO’s diagnostic system to monitor key parameters such as engine temperature, fuel efficiency, and vibrations.
Analyze trends: Use data trends from the system to identify any gradual power loss or wear in specific parts.
Receive real-time alerts: Set up alerts for any deviations from normal parameters to address potential problems before they affect performance.
Impact: Remote monitoring allows for quicker response times and targeted maintenance, minimizing power loss and reducing overall downtime.
3.5 Check Engine Compression and Perform Routine Engine Diagnostics
The engine is the heart of the tractor, and its compression is vital for ensuring that enough power is generated. Low compression can significantly reduce power output, so regular engine checks are essential to identify issues early.
Action Plan:
Test engine compression: Use a compression gauge to regularly test engine compression and identify any loss of pressure in the cylinders.
Check spark plugs and ignition systems: Worn-out spark plugs or ignition systems can lead to misfires and reduced power. Replace them regularly.
Monitor oil quality: Old or degraded engine oil can increase friction in the engine, leading to power loss and potential damage.
Impact: Regular engine diagnostics ensure that the engine operates at peak efficiency, preventing power loss and enhancing longevity.
3.6 Maintain the Hydraulic System
The hydraulic system is responsible for powering a variety of tractor functions. Hydraulic failure can lead to a loss of control over attachments, power steering, and more, resulting in power loss and reduced productivity.
Action Plan:
Inspect hydraulic fluid: Regularly check hydraulic fluid levels and ensure it is clean and free from contaminants.
Examine hoses and seals: Look for leaks or wear in hydraulic hoses and seals, which can cause fluid loss and inefficient operation.
Replace hydraulic filters: Replace hydraulic filters every 500 hours of operation or sooner if signs of contamination appear.
Impact: A well-maintained hydraulic system ensures that all tractor functions are working at full capacity, helping to avoid power loss.
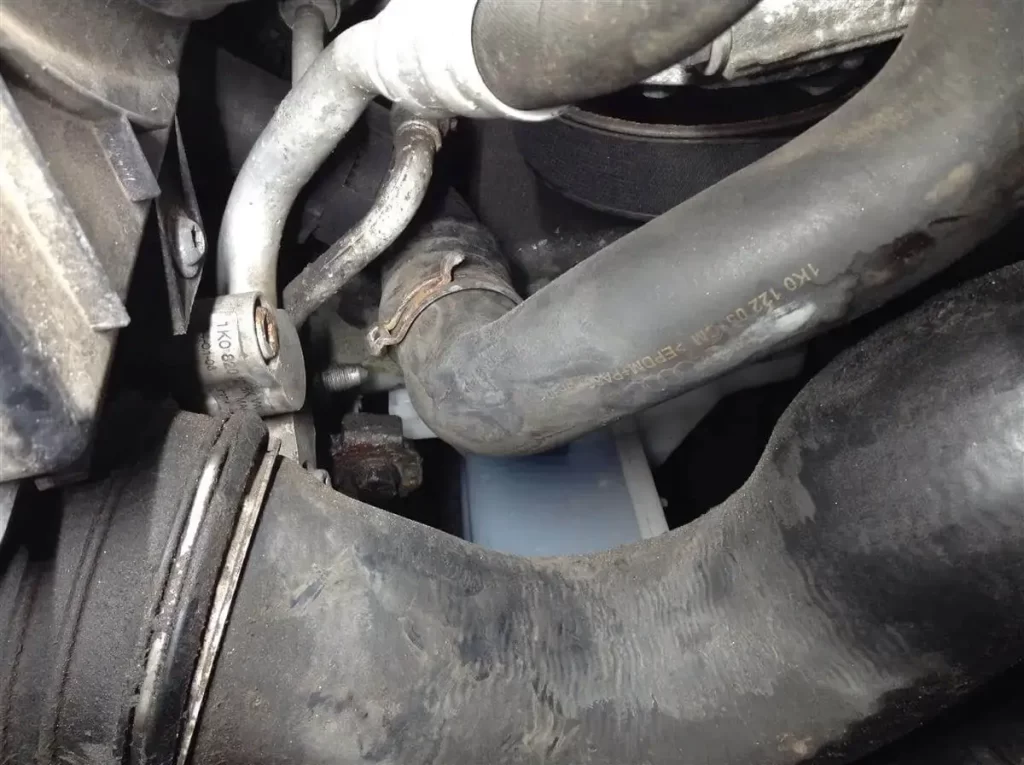
4. When to Replace vs. When to Repair: Decision Guide
Tractor maintenance decisions often hinge on a simple question: Should I replace a part, or is it still worth repairing? This dilemma arises when parts begin to show signs of wear but haven’t completely failed. However, making the right call is not always straightforward. Each part’s wear and tear, the severity of its damage, and the associated costs of repair versus replacement all come into play. In this section, we explore how to navigate this decision and offer insights on when to replace a part to prevent unnecessary downtime and costs.
4.1 Assessing Repair vs. Replacement Costs
Before making a decision, it’s essential to conduct a cost-benefit analysis. Sometimes, the repair cost is not worth it, especially when the part’s lifespan has been exhausted. On the other hand, some parts may be worth repairing if the damage is minor, and the part still has significant life left.
Action Plan:
Cost comparison: Compare the cost of repair to the cost of replacement, including labor and downtime. If the repair cost is 70% or more of the replacement cost, it may be better to replace the part.
Assess the lifespan: Consider how much life is left in the part. For example, if the part is near the end of its expected service life, replacing it might be more economical in the long run.
Impact: Making an informed decision on repair versus replacement can save you from unnecessary repairs and costly replacements before the part has fully worn out.
4.2 Long-Term Use vs. Sudden Failure
While some parts degrade over time with gradual wear and tear, others may fail suddenly. For parts that degrade slowly, repairs might offer a temporary solution, allowing you to extend their lifespan. However, for parts that tend to fail suddenly and catastrophically, it’s better to replace them before they cause major damage.
Action Plan:
Monitor part usage: Keep track of parts that show signs of gradual wear, like belts, air filters, or fuel injectors. If these parts show performance issues over time, a repair may suffice.
Preventive replacement: For critical parts such as the clutch plate or hydraulic hoses that are prone to sudden failure, it is better to replace them as soon as you see signs of wear.
Impact: This approach reduces the risk of sudden failures that lead to unexpected downtime, allowing for smoother operations and better planning.
4.3 When to Replace Parts for Safety
Certain tractor parts are responsible for operational safety. Parts such as brake pads, the hydraulic system, and the battery must be replaced when they begin to show any signs of damage, regardless of whether they can be repaired. A failure in any of these critical components can result in major safety hazards.
Action Plan:
Prioritize safety-critical parts: Always replace parts like brake pads, hydraulic hoses, or any worn-out component that could jeopardize the safety of the equipment and its operator.
Frequent inspections: Conduct regular safety checks to ensure no critical components have been overlooked. This will help you spot early signs of wear that can be addressed before they turn into a serious issue.
Impact: Prioritizing safety-critical replacements ensures that the tractor operates safely, reducing the risk of accidents, injury, or fatal failures.
4.4 Using MINNUO’s Remote Diagnostics to Guide Decisions
One of the key advantages of modern technology is the ability to monitor tractor systems remotely. MINNUO’s remote diagnostics platform offers real-time data that can alert you to early signs of wear or failure in components. This technology enables you to make more informed decisions about whether to repair or replace parts before power loss or other issues occur.
Action Plan:
Use the MINNUO diagnostic platform: Take advantage of the data provided by the system to monitor your tractor’s health. The system can provide alerts about system malfunctions, preventing further damage.
Plan preventive maintenance: By analyzing the data trends from MINNUO’s remote diagnostics, you can schedule timely replacements and repairs, ensuring that the parts are not replaced prematurely, but also not left to fail completely.
Impact: Using remote diagnostic tools helps you avoid unnecessary repairs and replacement, improving cost-effectiveness while maintaining high operational efficiency.
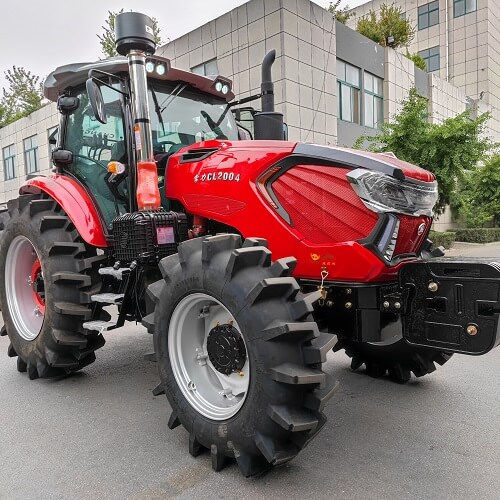
5. Case Studies: Solving Power Loss for Farmers Worldwide
In this section, we examine real-world case studies of how power loss issues in tractors have been addressed for farmers across various regions. These examples highlight the challenges faced, the solutions implemented, and the results achieved. The goal is to offer practical insights into the methods that can be used to resolve power loss problems and optimize tractor performance.
Case Study 1: South American Client – Air Intake System Upgrade for Improved Power Recovery
Challenge:
In South America, a large-scale agricultural operation was experiencing significant tractor power loss due to clogged air intake systems. This was especially problematic in areas with heavy dust accumulation, such as dry-field farming. The tractors were struggling to maintain consistent power, which delayed harvesting schedules and reduced operational efficiency.
Solution:
The client opted for a comprehensive upgrade to the air intake system. This involved the installation of high-efficiency air filters and pre-filters designed to handle extreme dust conditions. Additionally, the system was modified to include a regular maintenance schedule for cleaning and inspecting the air intake components.
Results:
After the upgrade, the tractors experienced an immediate improvement in power recovery and efficiency. The enhanced air filtration system significantly reduced engine strain, leading to smoother operations, fewer breakdowns, and a noticeable increase in productivity. The client reported a reduction in maintenance costs and a 20% increase in operational hours before the next maintenance cycle.
Case Study 2: Central Asia – MINNUO Remote Diagnostics for Fuel System Monitoring
Challenge:
A large farming enterprise in Central Asia faced ongoing issues with fuel system failures due to poor-quality fuel and inconsistent maintenance. This led to frequent power loss and engine misfires, especially during peak agricultural seasons when performance was critical. The local team struggled with detecting issues before they caused major breakdowns, resulting in high downtime and repair costs.
Solution:
The farm implemented MINNUO’s remote diagnostics platform, which provided real-time monitoring of the fuel system and other critical components. The system continuously tracked key parameters such as fuel flow, pressure, and temperature. Alerts were sent when irregularities were detected, enabling the team to perform targeted maintenance before power loss occurred.
Results:
The real-time data from MINNUO allowed the team to address fuel system issues proactively, preventing extended downtime. The system’s predictive analytics helped reduce maintenance costs by 15% and ensured that tractors maintained peak performance throughout the busy planting and harvesting seasons. The client also noted that the use of remote diagnostics streamlined their maintenance scheduling and reduced unnecessary part replacements.
Conclusion: Power Loss Is Preventable
In conclusion, 90% of tractor power loss issues can be traced back to avoidable mechanical failures. By understanding the underlying causes of these problems—such as fuel system issues, clogged air filters, hydraulic overloads, and excessive engine wear—you can take proactive steps to prevent significant power loss.
Timely and regular maintenance, combined with the use of high-quality, original parts, is key to extending the life of your tractor and ensuring optimal performance. Regular inspections, coupled with preventative measures such as smart diagnostics, are proven methods to minimize downtime and costly repairs.
MINNUO offers comprehensive solutions to help customers implement effective maintenance strategies, from tailored parts replacement packages to smart diagnostic systems that can predict potential failures before they disrupt operations. By choosing MINNUO’s reliable and advanced services, you ensure that your equipment remains efficient, productive, and ready for the demands of the field.