Tractors are built to work hard—but when critical components fail, productivity halts. Every minute of downtime caused by a worn-out filter, a broken belt, or a hydraulic leak can translate into delayed fieldwork, costly repairs, and labor inefficiency. Frequent replacement of certain parts isn’t just a maintenance nuisance—it’s a direct operational risk with real economic impact.
That’s why understanding the most commonly replaced tractor parts—and why they fail—is crucial. Farmers and equipment managers often ask: Which parts tend to break first? What causes these failures? How can we reduce replacements and extend service life? These questions are not only valid but essential for improving maintenance planning, minimizing downtime, and lowering long-term operational costs.
In this article, we break down the top 7 most frequently replaced tractor parts, explain the root causes behind their failure, and offer actionable strategies for extending their lifespan. If you’re looking to cut costs, boost reliability, and protect your investment—this guide is for you. Let’s dive in.
Contents
- 1 1. Engine Oil Filter — The First Line of Defense
- 2 2. Air Filter – Silent Killer of Engine Efficiency
- 3 3. Battery – Small Component, Big Downtime
- 4 4. Clutch Plate – Stress Under Load
- 5 5. Hydraulic Hose – High Pressure, High Risk
- 6 6. Drive Belt – Small Crack, Big Trouble
- 7 7. Brake Pads – Essential but Often Overlooked
- 8 8. How to Extend the Life of These Parts
- 9 Conclusion
1. Engine Oil Filter — The First Line of Defense
The engine oil cartridge, though small in size, is the first line of defense for healthy engine operation. Its job is to filter impurities, metal particles and combustion by-products from the lubricating oil, preventing these contaminants from circulating into the engine system and causing severe wear.
Why is it always the first to be replaced?
In the context of agricultural tractors operating under long-term high loads and harsh environments (e.g., dust, humidity, large temperature differences), the lubricant deteriorates quickly, and if the filter element is not replaced in time, the filtration efficiency decreases, and the impurities in the oil circuit come into direct contact with the bearings, pistons, valves, and other critical parts. This will not only lead to poor lubrication and increased engine heating, but also may cause major failures such as cylinder pulling and tile bursting.
What are the most common failure triggers?
Overloaded buildup of contaminants in the lubricant due to long replacement intervals
Use of low-quality filter elements with insufficient filtration precision and dirt-holding capacity
Missing or loose filter element seals, frequent opening of bypass valves
The solution: not only replacement, but also prevention.
Empirical data shows that most of the early engine wear is related to inadequate maintenance of the oil filter. Therefore, it is recommended that:
Strictly follow the cumulative hours of engine conditions to change regularly (e.g., every 250 hours)
Use original or certified high-efficiency filter elements (e.g., made of micro fiberglass material)
Synchronize lubricating oil change every time you change the filter element to ensure that lubrication systems are updated synchronously
Farming machines operating at high temperatures under heavy loads are recommended to shorten the replacement cycle and record the operating logs
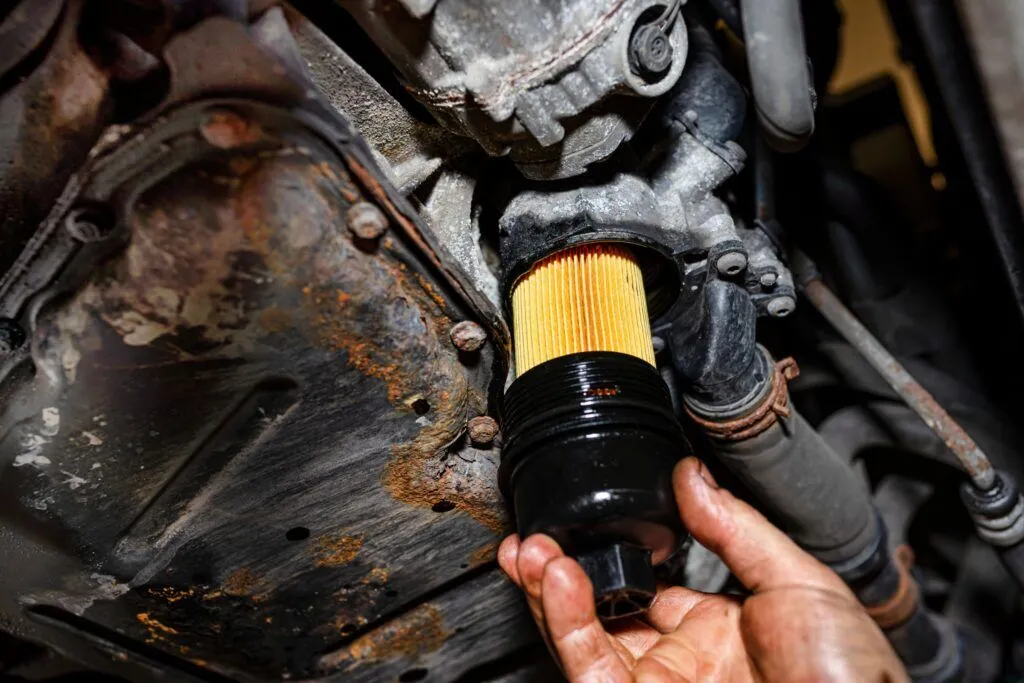
2. Air Filter – Silent Killer of Engine Efficiency
The air filter is like a human lung to the engine, filtering dust, sand and impurities in the air to ensure that the engine inhales clean air. In arid and dusty farmland, mining areas and construction zones, the air filter element bears a huge load.
Why is it an “invisible killer”?
Unlike oil or fuel filter element clogging will quickly appear alarm prompts, air filter element clogging is often manifested in reduced power, higher fuel consumption, engine running poorly, but many operators may not be immediately associated with the “air filter element”. As the resistance rises, the engine air intake is reduced, combustion efficiency decreases, accelerated carbon accumulation of parts and components, and in severe cases there will be black smoke, starting difficulties, blue smoke and other phenomena, affecting the engine life.
Sources of Common Problems:
Working in dust-intensive areas for a long time, such as dry-field farming, compost transportation
Not cleaning or replacing the filter element on a regular basis, and the filter element housing is even covered with mud and sand
Using a mismatched model or poor-quality filter element, with poor sealing, and dust enters into the intake tract bypassing the filter element
How to accurately prevent this?
Maintenance recommendations are as follows:
Check the air filter element every 100 hours of operation, and shorten it to 50 hours in severe dusty environments.
Use compressed air to blow the filter element from the inside to the outside (the pressure should not exceed 0.2MPa) to avoid secondary damage.
Clean the filter element no more than 5 times each time, and the filter element media may be aging after that number of times, and it should be replaced in time.
Pay attention to checking the sealing ring of the filter element and the housing of filter element to ensure that there is no breakage or loosening.
It is recommended to use a two-stage air filtration system (pre-filtering system). It is recommended to use a two-stage air filtration system (pre-filter + main filter) to cope with heavy working conditions.
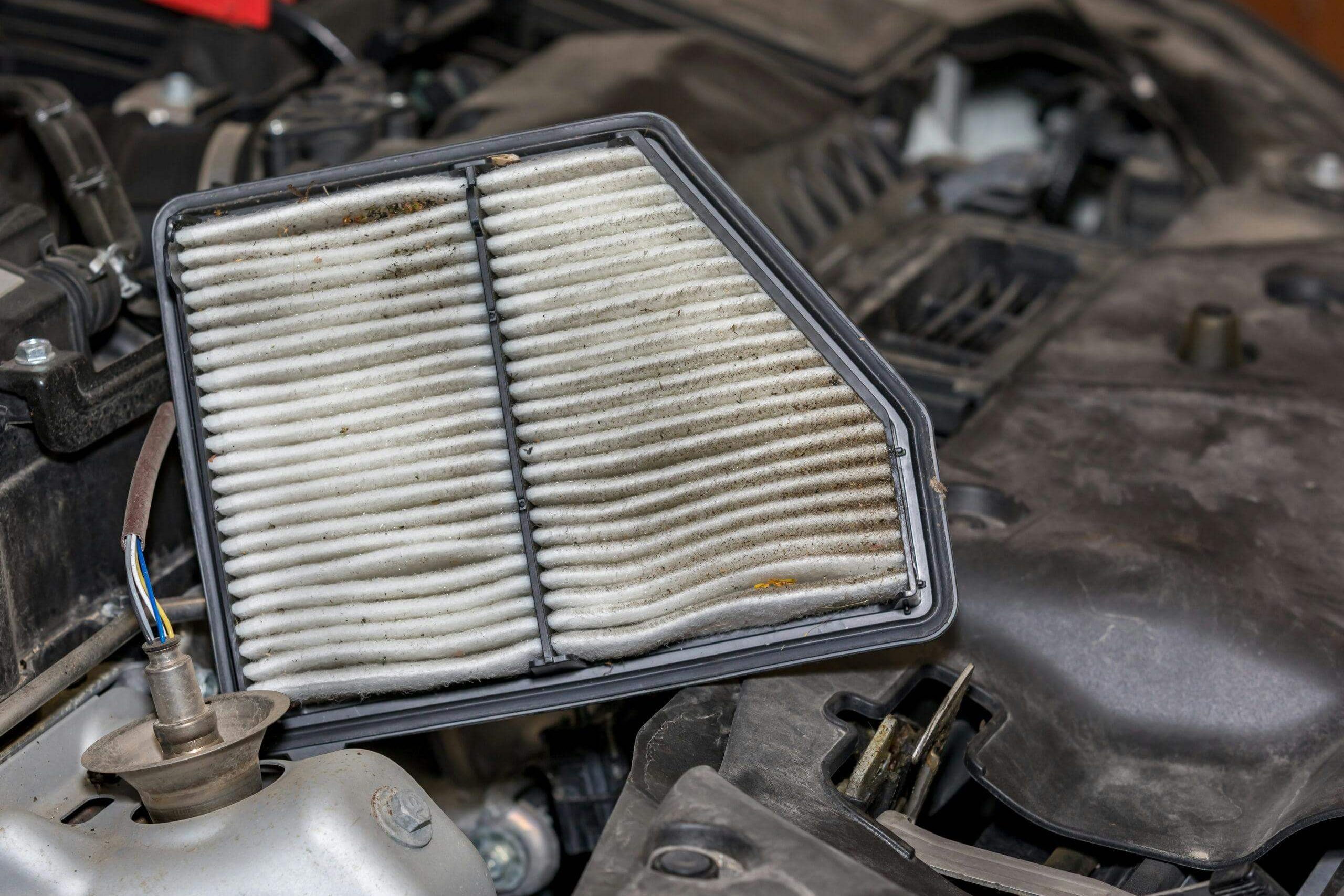
3. Battery – Small Component, Big Downtime
Don’t look at the size of the battery is not big, once the failure, not only delay the start, but also may lead to the whole machine paralyzed, the operation is interrupted. Especially in the spring and fall with a big temperature difference between morning and evening, cold winter, and long unused non-operating season, the battery is more “vulnerable link”.
Common causes of failure:
Sudden change in temperature: electrolyte viscosity rises at low temperatures, decreasing the ability to store electricity, starting current is insufficient;
Charging system aging: generator voltage abnormality or rectifier damage, resulting in insufficient charging;
Long-time parking: the tractor is parked in the winter for several months without start-up, slow discharging leads to the battery “depth of loss of power”;
Loose or corroded wiring Loose or corroded wires: resulting in poor current transmission, it seems that the battery is bad, but in fact, it is poor contact;
The impact of the failure is far more than just “can’t start”:
Can’t start in the morning, delaying the window period of agricultural affairs, especially in the rush to rush to the harvest stage of the impact is huge;
Repeatedly ignited and discharged, accelerating the aging of the battery and even burned the starter motor;
The use of voltage is insufficient, affecting Electromechanical control systems such as fuel injection, monitoring instruments, solenoid valves work abnormally;
✅ Practical maintenance recommendations:
1. Voltage regular check:
Monthly use a multimeter to detect the static voltage (full power should be ≥ 12.6V), if found below 12.2V should be supplemented with electricity in a timely manner;
2. Keep clean and dry:
Electrode staking should be cleaned of oxidation on a regular basis, and antioxidant grease can be coated to prevent corrosion, and the connection should be tightened and no loosening;
3. Winter Insulation treatment:
Below 20℃, it is recommended to use the battery thermal insulation cover or indoor parking to avoid the cold leading to battery icing failure;
4. Avoid over-discharge:
Disconnect the negative electrode of the battery for a long time without using it, or use the smart float charger to maintain the power;
Technician’s Tips:
“Battery loss of power” may seem like a small problem, but in the mountainous areas, suburbs and other areas of resource constraints, there is no way to find a replacement battery or a temporary hitch. It is extremely difficult to find a replacement battery or temporary power supply.
It is recommended that users do a whole vehicle circuit check before the season, and at the same time, make a record of the battery’s service life (generally 2~3 years) to avoid sudden shutdowns.
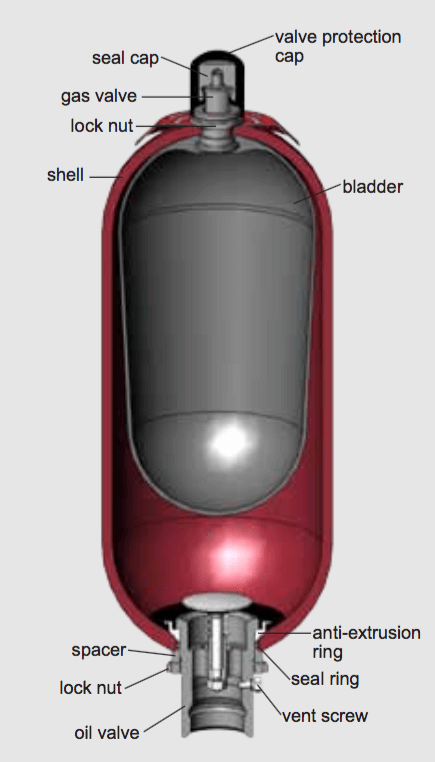
4. Clutch Plate – Stress Under Load
Although the clutch plate is not the “main character” of the engine, it is the key link of transmission efficiency. Once the failure, not only slippage and oil, but also directly affect the quality of tractor farming and operational rhythm. Busy season, “clutch a loose punch, half clutch on the burn” phenomenon is common, the reasons behind it is worth looking into.
⚠ Common reasons for wear and tear
Long-term overload operation: the use of agricultural implements exceeding the rated horsepower or deep plowing operations, increasing the friction load of the clutch plate;
Frequent shifting or reversing: Especially in small plots of land, curved, dense areas of work, frequent starting or gear, clutch plate wear increased;
Operating habits are not standardized:
Long-time half linkage (such as half-pressing the clutch to control the speed);
Frequent “double-pressing Frequent “double-pressing” of the clutch, frequent reaction of the clutch spring;
Oil or dust intrusion into the clutch cavity: resulting in slippage or reduced grip after contamination of the friction plate;
Failure Performance and Chain Reaction
Power transmission is not smooth: even if you add gas, the speed is slow to increase;
Starting slippage, noise: especially more obvious on ramps or towing operations;
Increased fuel consumption and reduced efficiency: the actual operating time is extended, and the unit area consumption time increases; in severe cases, the clutch spring will react more frequently. Increased fuel consumption and reduced efficiency: the actual working time is longer, and the time consumption per unit area increases;
In serious cases, the “burnt piece” smokes, and must be disassembled and replaced, which delays the farming time;
Maintenance and prevention suggestions
1. Control the working load:
Before the operation, make clear the matching power between the tractor and the farm implements, avoiding the “big vehicle with a small horse-drawn carriage”;
Special operations (plowing and deep pine) should be combined with low-speed gears and reasonable operation. For special operations (plowing and deep pine planting), the tractor should be equipped with low-speed gears and operated reasonably.
2. Improve driving operation:
Start crisply and neatly, and avoid half-linkage dragging gears.
Avoid frequent small-range turnarounds or in-situ shifting of gears, and recommend the use of a “zig-zag” operation route plan to reduce ineffective operation.
3. Regular inspection and maintenance:
Check the free travel of the clutch pedal and the adjusting nut quarterly to ensure that the linkage is flexible. Flexible;
Check the clutch housing for dust or oil seepage, clean and replace the oil seal if necessary;
4. Newbie training should not be neglected:
The reason for the early death of many clutch discs is not the quality, but the non-standardized operation;
On-site demonstration and training for new drivers is the key to guarantee the life of clutch discs;
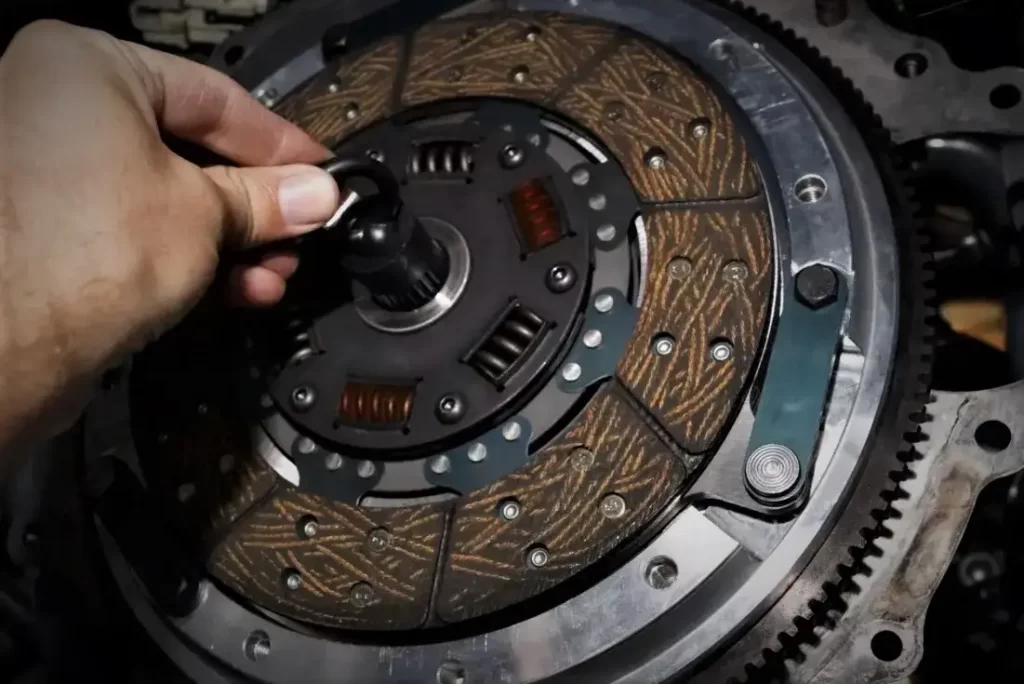
5. Hydraulic Hose – High Pressure, High Risk
Hydraulic hose is the “artery” of pressure transmission in the hydraulic system of agricultural machinery, once burst, it may lead to oil leakage in the light of downtime, or lead to the loss of control of hydraulics and injuries. In the high intensity frequency of operation and complex environment intertwined with the working conditions of the farm, this hidden danger especially need to be vigilant.
Vulnerability reasons:
Long-term high-pressure impact: repeated starting and stopping of the hydraulic system, load fluctuations, so that the internal rubber layer of the hose fatigue;
aging or corrosion of the joints: especially fittings and metal connections, prone to oil seepage or fracture;
installation of the bending radius is too small: the hose is forcibly “broken” or knot, resulting in the internal steel wire layer fracture;
environmental erosion:
Environmental erosion: the phosphorus and potassium in farmland soil is corrosive;
high temperature sun exposure makes the outer rubber layer harden and crack;
not regularly checked and replaced: many users “use it until it leaks”, resulting in accidents and hidden dangers;
Typical failures and consequences of
oil leaks are serious, the hydraulic system does not respond to the ploughing depth, lifting, steering and other functions are paralysed;
Hydraulic oil splashing: the high-pressure spray has a cutting effect, which can easily burn the skin or contaminate the hydraulic system. Splashing of hydraulic oil: high pressure spray with cutting, easy to burn the skin or pollute the farmland;
Sudden breakage leading to the whole vehicle flinging: sudden tilting or unstable lifting of the vehicle during operation, endangering the safety;
Preventive and Daily Management Recommendations
✅ Visually check the status of the hose before each operation:
Observe whether there is bulging, cracking, oil stains, oil seepage at the joints, and shut down immediately to deal with the problem;
✅ Strictly comply with the requirements of the bending radius when installing the hose:
Avoid forcible bending, and recommend the use of 90 ° or 45 ° metal elbows instead of over-expanding the hose. 45° metal elbow, instead of excessive bending of the hose layout;
✅ Regular replacement schedule:
Normal operating environment, replace the high-pressure hose every 24 months;
High temperature, heavy load or corrosive environment, it is recommended to shorten the period to 12 ~ 18 months;
Replacement at the same time to check the quality of the hydraulic oil and the cartridge whether there are impurities in the contamination;
✅ Standardization of the direction of the hose and fixing:
Hose should be laid along the body of the natural direction of the layout, with the clamps or brackets, to avoid the operation of swinging friction fixed, to avoid swinging and rubbing. Fixed, to avoid swinging friction during operation;
First-line use of the recommendations:
“Hose bulging, does not mean that it can still last a day.”
Field maintenance, 90% of the hydraulic burst accidents occurred in the “look still work” on the hose.
It is recommended that the use of high temperature, corrosion-resistant outer rubber layer of the hose products, give preference to models with a bursting protection sleeve, to enhance the overall use of the safety level.
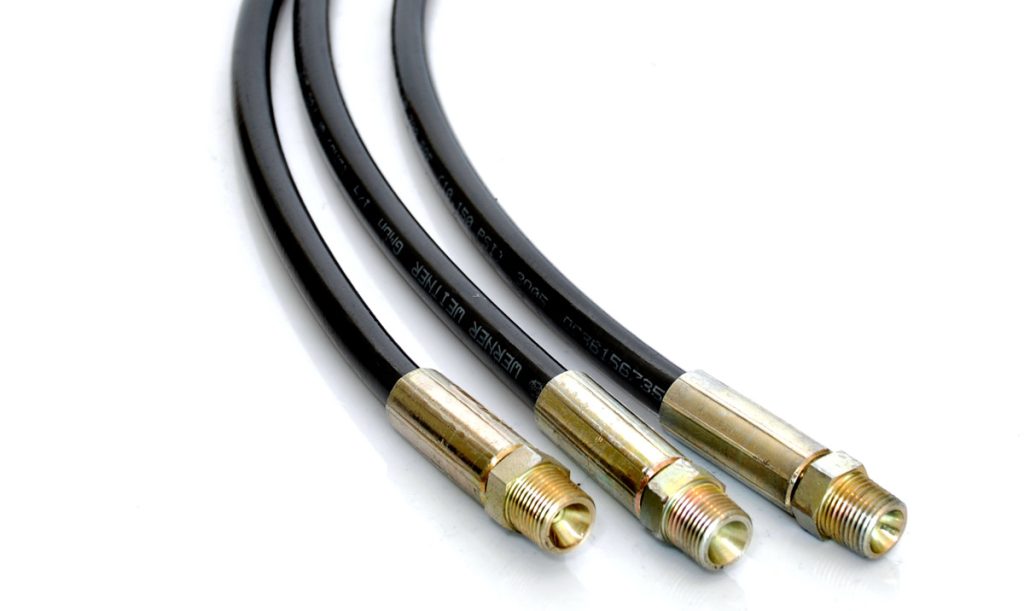
6. Drive Belt – Small Crack, Big Trouble
The drive belt is small, but it is a critical node in the powertrain. A crack may cause the whole situation to be “paralyzed”.
In-depth analysis of common problems
Two manifestations of improper tension:
too loose tension → belt slippage, increased heat, drive efficiency decline;
too tight tension → abnormal shaft bearing force, early cracking of the belt.
Material aging is not only look at the “age”:
long-term exposure to high temperature, high humidity, dusty environment, the rubber layer of the belt will gradually lose elasticity, micro-cracks and delamination phenomenon, even if the use of infrequent also need to be replaced.
Mismatched fittings are also a hidden danger:
The use of non-original belts, size or groove type deviation, will lead to belt offset, groove nibbling or even fall off.
Chain reaction of failure at the touch of a button
Once the drive belt cracks or breaks, it may cause:
Generator failure → battery power loss, the whole machine can not be started;
water pump stops → engine cooling failure, resulting in high temperature cylinder;
air-conditioning system paralyzed → poor driving environment in summer, the driver is easy to fatigue;
oil pressure system abnormality → unstable operation of the hydraulic device, affecting the safety of the working conditions.
✅ Suggested Practice: Shift from Reactive Replacement to Proactive Prevention
Regular Spot Inspection Three-Step Method:
Visual Inspection (once a week)
Look for abnormalities such as cracks, bulging, delamination, edge wear, and so on.
Hand Pressure Inspection (every 100 hours or maintenance period)
Check for even rebound by gently pressing the center with your hand; use a tensiometer for more accuracy.
Audible identification
If there is a sharp whistling sound at the moment of starting, you should focus on checking the tension and pulley wear.
Replacement Suggestion:
Usually replace every 600-1000 hours, or early warning according to the model manual;
High temperature working conditions suggest using heat-resistant composite material belt with oil and dust resistant design.
PRO TIP
“Once a drivetrain breaks down, it’s not as simple as replacing a belt, it can come with a whole set of repairs and downtime losses.”
Before high-frequency operations such as spring planting and fall harvesting, it is recommended to carry out a special inspection of the transmission system;
For users with high operational intensity, consider installing belt status sensors to monitor tension and wear status in real time.
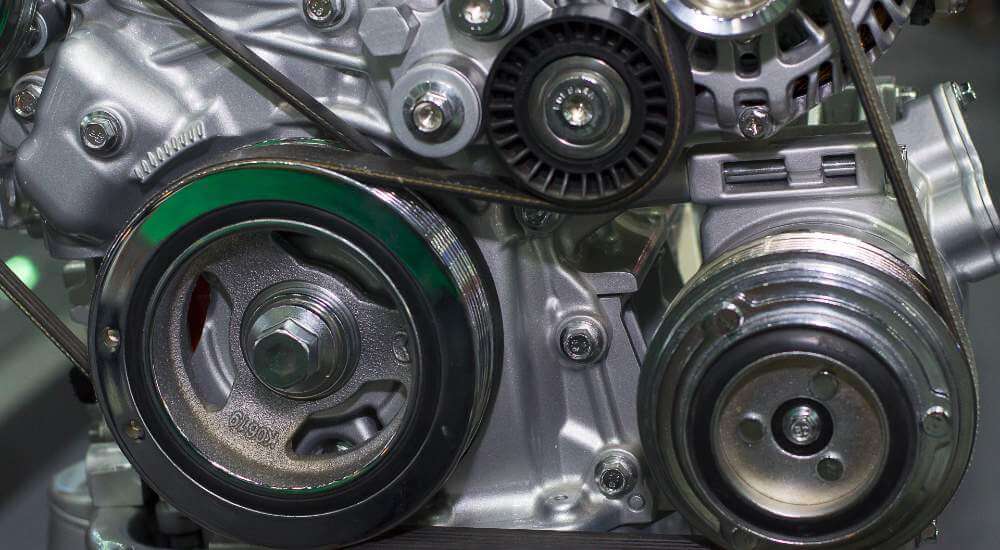
7. Brake Pads – Essential but Often Overlooked
The braking system is the last line of defense, and brake pads are its most overlooked consumable. If something goes wrong, it’s not just a “scuffing sound”, it’s a safety warning.
Risks of neglected usage scenarios
Brake pads wear out much faster on muddy and sloping terrain than on regular dry ground. Dust particles, gravel, corrosive mud, etc. can penetrate into the braking system, resulting in:
Rapid thinning of the brake pads
Uneven wear and unilateral clutching
Localized overheating or even deformation of the brake discs
Behind the “soft brakes” lies a hard risk
On the surface it only looks like the braking distance is getting longer, but in reality it’s:
Difficulty in stopping the machine at short distances under heavy load, especially dangerous on downhill slopes or during towing operations; the driver’s safety is at risk. It is especially dangerous in downhill or towing operations;
Drivers need to apply the brakes more vigorously, which makes them fatigued and unresponsive during long hours of operation;
In extreme cases, the braking system fails due to overheating, leading to loss of control of the entire vehicle.
How to recognize early wear?
Visual inspection: Normal brake pad thickness is about 10~12mm, below 5mm should be planned for replacement; below 3mm belongs to the “red line” and must be replaced immediately.
Sound identification: the appearance of “metal friction sound” or “sharp whistle”, usually alarm pads to remind the imminent exhaustion.
Foot feedback: A “soft” brake application or a longer travel time to slow down indicates a decrease in brake efficiency.
Brake Powder: A large amount of black brake powder deposits on the inside of the wheel hub indicates that the brake pads are wearing out fast.
✅ Maintenance advice: intervene rather than wait for it to make a noise
Set inspection intervals: It is recommended that the brake system be inspected after every 250 hours of operation; shortened to 150 hours for equipment that operates frequently in mud.
Check brake discs and calipers in tandem: Some brake pad wear is not simply exhaustion, but rather rapid reduction due to disc “bite”, so be sure to check the wear track and disc surface temperature difference at the same time.
Record the length and frequency of use: During intensive operation, a daily log can help to estimate the life of the brake pads and make it more scientific to make spare parts in advance.
Replacement suggestion: It is recommended to choose original or high-temperature wear-resistant brake pads, avoid using cheap and inferior materials, which may lead to brake failure or disc damage.
Feedback from the front line – User Facts
“One of our rollers nearly overturned when the brake pads melted due to overheating during continuous downhill operation, resulting in complete brake failure. Later, the brake system was checked weekly and replaced with high-temperature wear-resistant brake pads, and there were no more problems.”
— Head of an engineering team in Indonesia
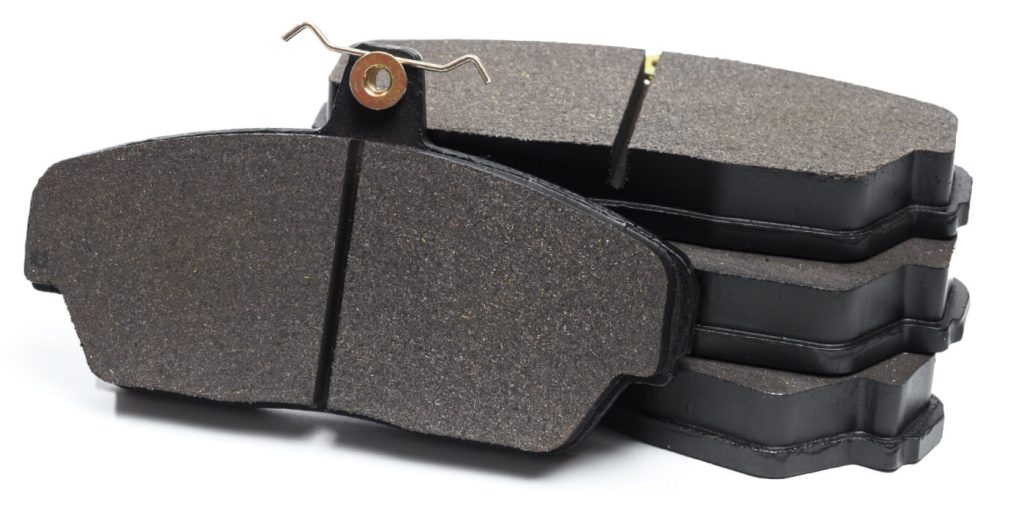
8. How to Extend the Life of These Parts
Tractor components wear out-some faster than others. But wear ≠ waste. Through a combination of good practices, smart technology, and quality choices, their lifespan can be extended significantly. Through a combination of good practices, smart technology, and quality choices, their lifespan can be extended significantly.
Regular spot checks are more than just a “look-see”
The root cause of early wear and tear on most equipment is not high strength, but “breaking down quietly. The root cause of early wear and tear in most equipment is not strength, but rather the fact that it “breaks down silently”. The following three steps are recommended to build a truly effective inspection system:
Create an inspection checklist: cover high-risk areas such as hydraulics, air intake, brakes, etc. Tick off each inspection and take responsibility for it. Record each inspection with a check mark and responsibility.
Record the hours of use of key parts: such as air filters, brake pads, etc. to set up the “replacement of prerequisite reminders”, and set up early warning signs (such as color stickers or electronic records).
Compare the trend of inspection results: Instead of discovering anomalies at once, analyze the curve of changes in thickness, pressure, vibration, etc., and determine whether it is gradually failing.
Tips: Inspection ≠ maintenance, a regular look is not the purpose, early replacement is the real key to save maintenance costs.
Original parts ≠ expensive parts, is the “can not afford” protection
Cottage parts, although cheap, but the tolerance is large, poor compatibility, such as poor quality filter may cause lubrication is not smooth, the air filter screen is too loose directly into the cylinder impurities, the loss is not worth the gain.
High-intensity operation is recommended to use industrial-grade parts, such as high-temperature area is recommended to use heat-resistant seals, heavy-duty traction is recommended to choose the mandatory lubrication structure of the bearing system.
Pay attention to the systematic matching between the components, different brands of components may lead to deviation from the operating parameters of the system, such as different specifications of the hydraulic line connector, easy to produce leaks.
Intelligent system intervention: truly “useful” prognosis, not a show-off
Nowadays, more and more users of agricultural machinery are choosing to access remote intelligent diagnostic systems. For example:
MINNUO remote platform supports oil temperature, voltage, vibration trend data transmission, once the abnormal parameters jump can be remotely reminded of maintenance, to avoid the whole machine “work with disease”.
Combined with the AI prediction model, it can automatically analyze whether the machine is in abnormal working conditions, such as “the noise of a motor bearing has increased by more than 15%” and trigger an alarm.
It realizes “off-site monitoring”, which is especially suitable for agricultural enterprises with multi-location operation and off-site management. Improve maintenance response speed and reduce downtime costs due to waiting for parts.
✅ Hands-On Advice – Tips for Extending Service Life
Components | Examples of life extension techniques |
Air Filter | Clean dust immediately before and after operation in dusty places, use pre-filter or dust cover if necessary |
Oil Filter | Shorten the replacement cycle appropriately in high temperature seasons, use high temperature resistant models |
Brake Pads | Avoid flushing water directly to cool down after operation to prevent cracks caused by thermal stress |
Hydraulic Hoses | Flexibility test every year, even if there are no cracks for more than 3 years, it is also recommended to replace them to prevent aging and breakage |
Battery & Connectors | Clean up oxidized layer once a month, and coat ports with insulating grease to prevent corrosion; in winter, charge in advance to avoid voltage starting difficulties. |
Conclusion
From air filters clogged by dust, to brake pads worn down by load and terrain, each frequently replaced tractor part teaches a lesson: most failures start long before they’re visible.
This article reviewed the seven most commonly replaced tractor parts—air filters, oil filters, brake pads, hydraulic hoses, battery terminals, fan belts, and fuel injectors—highlighting how contamination, heat, vibration, and poor-quality parts contribute to premature wear.
What matters most isn’t how fast you replace them, but how early you prevent their failure.
Regular inspections, predictive maintenance, and component compatibility go further than reactive repairs. Long-term efficiency starts with smart investment in care.
MINNUO offers tailored maintenance kits and part replacement packages designed for your tractor model and working environment, helping you reduce unplanned downtime and maintenance costs—so your equipment keeps working as hard as you do.