Tractors are a vital component of modern farming, and their hydraulic systems play an essential role in the effective operation of many attachments such as loaders, plows, and other implements. The hydraulic system is responsible for providing the necessary power to perform various tasks, making it a critical part of the tractor’s overall performance. Given its importance, maintaining a healthy hydraulic system is crucial for efficient operation and avoiding unexpected disruptions in the field.
Hydraulic system failures can cause significant operational setbacks, including costly repairs, long downtimes, and reduced productivity. When the hydraulic system malfunctions, it can lead to a loss of functionality in the attachments, which delays work, increases labor costs, and impacts the overall efficiency of farming operations. Furthermore, hydraulic system failures may require expensive repairs or part replacements, which can severely affect a farm’s bottom line.
This article focuses on providing practical steps for extending the lifespan of your tractor’s hydraulic system. By improving system efficiency and adopting maintenance practices that minimize the risk of failure, farmers can reduce long-term operational costs and ensure their tractors remain in top condition. Keep reading to discover actionable strategies for maintaining a healthy hydraulic system and preventing costly breakdowns in the future.
Contents
- 1 1. Common Issues in Tractor Hydraulic Systems and Their Impact
- 2 2. Preventive Maintenance Practices for Extending Hydraulic System Life
- 3 3. Using Technology to Improve Hydraulic System Efficiency
- 4 4. Optimal Operating Practices to Reduce Hydraulic System Stress
- 5 5. Case Studies: Real-Life Examples of Hydraulic System Maintenance Success
- 6 FAQ
1. Common Issues in Tractor Hydraulic Systems and Their Impact
Tractor hydraulic systems are essential for powering attachments and ensuring smooth operation. However, several common issues can significantly impact system performance, leading to costly downtime, repairs, and inefficiency. Understanding these issues is the first step toward maintaining and extending the life of your equipment.
1.1 Hydraulic Fluid Contamination
Hydraulic fluid plays a vital role in ensuring the efficient operation of hydraulic systems. When contaminants like dirt, moisture, and debris get into the hydraulic fluid, it can cause severe damage to system components, including pumps, motors, and valves.
Common Causes:
Improper Sealing: Worn or damaged seals can allow dirt and moisture to enter the system, contaminating the fluid.
Poor Fluid Storage: Storing hydraulic fluid improperly, where it’s exposed to moisture and debris, can lead to contamination.
Dirty Filters: Over time, filters become clogged and lose their ability to effectively capture contaminants.
Consequences:
Increased Wear: Contaminated fluid causes metal particles to circulate through the system, leading to faster wear on critical components.
Rust and Corrosion: Moisture in the hydraulic fluid can cause rust on metal parts, leading to failure and poor system performance.
1.2 Leaks and Pressure Loss
Leaks are a frequent issue in tractor hydraulic systems. These leaks may be caused by worn seals, damaged hoses, or faulty valves. Leaks can lead to a significant loss in hydraulic pressure, resulting in underperformance or even system failure.
Common Causes:
Worn or Damaged Seals: Seals naturally wear out over time, creating gaps for fluid to escape.
Hoses and Fittings: Cracked hoses or loose fittings can allow fluid to leak, reducing system pressure and efficiency.
Faulty Valves: Over time, valves can deteriorate or become clogged, causing them to malfunction and lead to pressure loss.
Consequences:
Reduced System Performance: Pressure loss results in slow or unresponsive hydraulic movements, making it difficult to operate attachments effectively.
Increased Fuel Consumption: The system will require more power to compensate for lost pressure, leading to increased fuel usage.
Potential System Failures: If pressure loss goes undetected, it can lead to further damage to pumps, motors, and other key components.
1.3 Overheating
Overheating is a common issue in tractor hydraulic systems, especially under heavy loads or in high-temperature environments. Hydraulic fluid is designed to operate within a specific temperature range, and exceeding that range can cause the fluid to lose its viscosity, reducing its effectiveness.
Common Causes:
Excessive Load: Operating under high pressure or with too many attachments can generate more heat than the system is designed to handle.
Poor Cooling: The radiator or cooler may be clogged, reducing its ability to dissipate heat.
Low Fluid Levels: Low fluid levels cause the hydraulic pump to work harder, leading to increased temperatures.
Consequences:
Reduced Efficiency: Overheating can cause the fluid to lose viscosity, making it less effective at lubricating and transferring power.
Component Damage: Prolonged overheating can lead to permanent damage to seals, valves, and the hydraulic pump.
Increased Wear: Heat accelerates the wear and tear on system components, shortening their lifespan.
1.4 Excessive Wear on Pumps and Motors
Pumps and motors are the heart of the hydraulic system, and their failure can lead to complete loss of hydraulic function. Regular wear on these components is normal, but excessive wear can be caused by poor maintenance practices, improper fluid levels, or using the system beyond its design limits.
Common Causes:
Improper Fluid Levels: Low or contaminated fluid can cause the pump to work harder, leading to excessive wear.
Overloading: Using the hydraulic system for tasks that exceed its capacity can cause the pump and motor to overheat and fail prematurely.
Lack of Regular Maintenance: Not performing routine checks and cleaning can cause parts to deteriorate more quickly.
Consequences:
Complete Hydraulic Failure: Worn-out pumps or motors may cease to function, leading to the loss of the ability to power attachments or perform critical tasks.
Reduced System Efficiency: Worn pumps and motors can lead to inefficient energy use, resulting in higher fuel consumption and lower productivity.
Expensive Repairs: If left unchecked, worn components can cause extensive damage to the hydraulic system, leading to costly repairs or replacements.
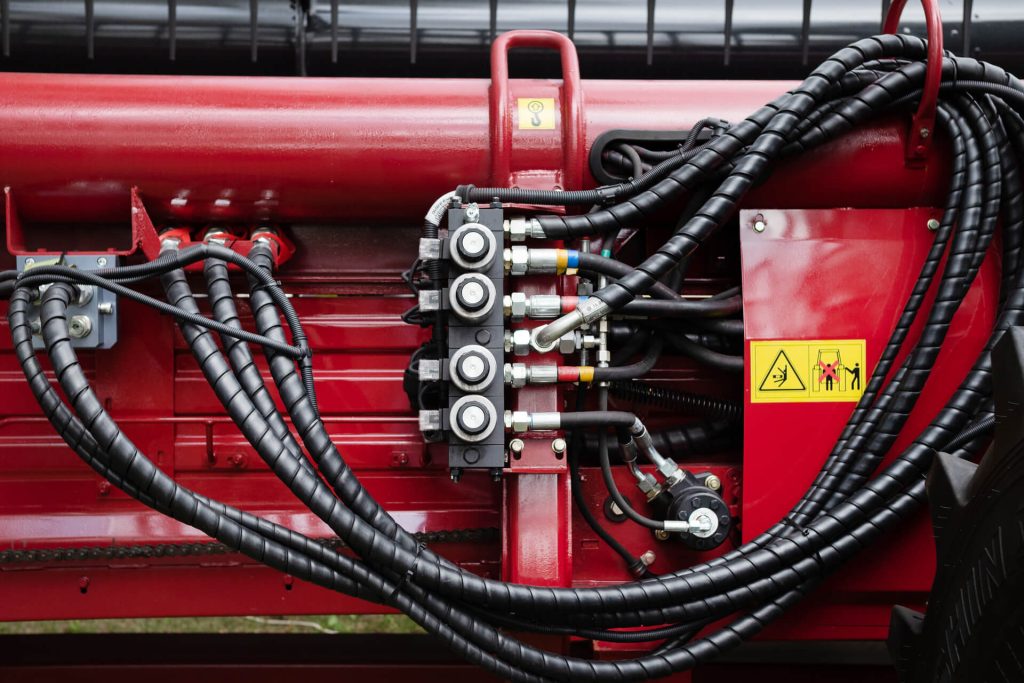
2. Preventive Maintenance Practices for Extending Hydraulic System Life
Maintaining the hydraulic system of your tractor is vital to ensure its efficient operation and longevity. With regular maintenance, many issues like system failures, leaks, or premature wear can be avoided. Below are effective and practical maintenance practices that will help extend the life of your tractor’s hydraulic system.
2.1 Regular Fluid Checks and Changes
Hydraulic fluid is the lifeblood of the system, and maintaining its quality is crucial for optimal system performance. Over time, fluid degrades due to contaminants and heat, which can significantly impair the efficiency of the system.
Key Points:
Importance of High-Quality Hydraulic Fluid: Using high-quality hydraulic fluid designed for your tractor’s specific needs ensures better performance and longer component life. Always check that the fluid meets the manufacturer’s specifications.
Recommended Fluid Check Intervals: Perform fluid checks based on the tractor’s operating conditions. In normal conditions, check the fluid level every 50–100 hours of use. However, in harsher environments, such as dusty fields or extreme temperatures, increase the frequency of fluid inspections.
Fluid Change Guidelines: Change the hydraulic fluid at regular intervals (often every 500–1000 hours of operation), as recommended by the manufacturer. Delaying fluid changes can cause buildup of contaminants, reducing fluid effectiveness and causing system damage.
2.2 Filter Maintenance and Replacement
Filters play a crucial role in maintaining the cleanliness of the hydraulic fluid by removing dirt, debris, and particles that could otherwise cause significant damage to the system’s components.
Key Points:
Role of Filters: Filters prevent contaminants from circulating through the hydraulic system, helping to protect the pumps, valves, and seals from wear and failure.
Inspection and Timely Replacement: Regularly inspect the hydraulic filters for signs of clogging or contamination. Replace filters at recommended intervals or more frequently if the tractor is used in harsh conditions.
Types of Filters: Use the correct type of filter as specified in the tractor’s manual. The two main types are suction filters (for large particles) and pressure filters (to protect against fine particles). Both should be checked and replaced periodically.
2.3 Monitor Fluid Levels and Pressure
Maintaining the correct fluid levels and pressure is critical for ensuring that your tractor’s hydraulic system operates smoothly and efficiently. Both low fluid levels and improper pressure can cause excessive wear and even system failure.
Key Points:
Correct Fluid Levels: Always keep the hydraulic fluid at the level indicated by the manufacturer. Low fluid levels can cause air to enter the system, leading to inefficient operation and increased wear.
Pressure Monitoring: Proper pressure is essential to ensuring the system operates at peak efficiency. Low or high pressure can strain the system, leading to overheating, pump failure, or leaks.
Why It’s Critical for Performance: Maintaining proper fluid levels and pressure ensures that hydraulic components like pumps and cylinders receive the necessary lubrication and force, minimizing wear and preventing premature failures.
2.4 Inspect for Leaks Regularly
Leaks in the hydraulic system can lead to significant losses in fluid, which not only affects the performance but also results in costly downtime and repairs. Regular inspection for leaks is essential to preventing long-term damage to the tractor’s hydraulic system.
Key Points:
How to Check for Leaks: Regularly inspect hoses, seals, and connections for signs of leakage. Look for oil stains on the tractor or ground and check around fittings for wetness.
Costly Consequences of Leaks: A small leak can result in the loss of hydraulic fluid, reducing the system’s efficiency. In severe cases, it can lead to total system failure.
Best Practices for Early Leak Detection: Inspect the system during routine maintenance, and make sure to use pressure tests to identify hidden leaks, especially in hard-to-reach areas like underbelly or joints.
2.5 Prevent Overloading and Excessive Wear
Excessive strain on the hydraulic system can lead to overheating, wear on key components, and reduced system life. It’s important to avoid overloading the tractor or the hydraulic system beyond its designed capacity.
Key Points:
Importance of Maintaining Proper Load: Ensure that the tractor is always within its rated load capacity. Overloading the tractor can lead to hydraulic failure, excessive fuel consumption, and accelerated wear on the system.
Prevention of Overuse: Avoid running the system for extended periods without breaks. Constant use of the hydraulic system without adequate cooling can lead to overheating and component damage.
3. Using Technology to Improve Hydraulic System Efficiency
Technological advancements are revolutionizing the way we manage and maintain hydraulic systems. By leveraging modern tools and remote monitoring systems, farmers and equipment managers can drastically improve the efficiency and longevity of their tractors’ hydraulic systems. In this section, we’ll explore how technology can help identify problems earlier, reduce downtime, and optimize overall system performance.
3.1 Remote Monitoring and Diagnostics
Remote monitoring systems have become an invaluable tool for preventing system failures and improving hydraulic efficiency. Through real-time data collection, these systems offer insight into the performance of hydraulic systems, allowing for proactive maintenance decisions.
Key Points:
How MINNUO’s Remote Diagnostics System Works: MINNUO offers a cutting-edge remote diagnostics platform that tracks hydraulic system performance in real-time. The system collects data on various parameters such as fluid temperature, pressure levels, pump performance, and fluid flow rates. By constantly monitoring these factors, the system can detect irregularities that may indicate an impending failure.
Predictive Maintenance Benefits: One of the major advantages of using real-time data is predictive maintenance. Instead of reacting to failures when they occur, the system can predict potential issues before they lead to breakdowns. For instance, if the system detects a decrease in hydraulic pressure, it can send an alert, prompting you to inspect the system before the problem escalates.
Reducing Downtime and Extending System Life: Early detection of problems not only prevents costly repairs but also reduces the amount of downtime. Knowing the exact condition of the hydraulic system allows for timely interventions that can extend the overall life of the equipment, saving both time and money in the long run.
3.2 Hydraulic Fluid Condition Monitoring
Maintaining proper hydraulic fluid condition is essential for ensuring that the system operates at peak efficiency. Monitoring the fluid’s viscosity, temperature, and contamination levels can help identify potential issues that could affect system performance.
Key Points:
Fluid Condition Measurement Tools: Modern technology provides tools that help measure the condition of hydraulic fluid accurately. These include sensors for monitoring viscosity, particle counters for contamination levels, and thermal sensors for fluid temperature. The use of these sensors enables equipment managers to ensure that the fluid is in optimal condition.
Why Fluid Condition Matters: Hydraulic fluid plays a pivotal role in the performance of the hydraulic system. If the fluid is too thick (high viscosity) or too thin (low viscosity), it can reduce the system’s efficiency, cause excessive wear on components, and even lead to pump failure. Contaminants such as dirt, water, or debris can further exacerbate the problem, causing wear, rust, and clogging.
Continuous Monitoring for Optimal Performance: Continuous monitoring allows for real-time tracking of fluid health. If the fluid’s viscosity changes or contamination levels rise, it triggers an automatic alert, prompting the need for a fluid change or filter replacement. By maintaining clean and appropriately viscous fluid, you can significantly improve the hydraulic system’s performance and longevity.
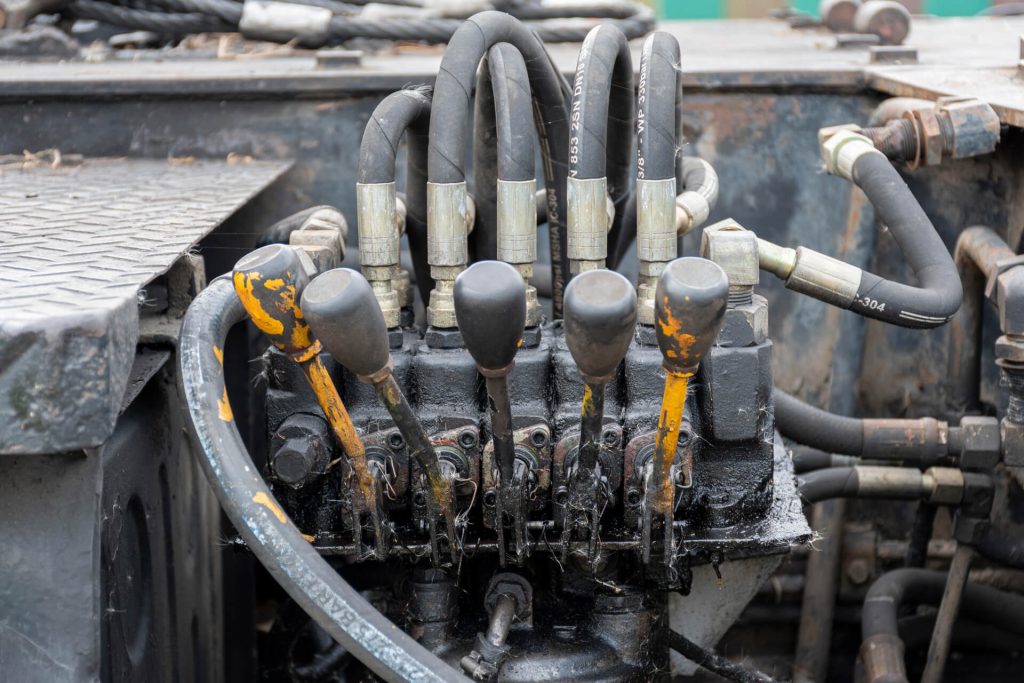
4. Optimal Operating Practices to Reduce Hydraulic System Stress
Maintaining hydraulic systems requires not only regular maintenance but also careful attention to operational practices. By adopting proper operating techniques, farmers and equipment operators can significantly reduce the strain placed on hydraulic systems, thus extending the life of their machinery and improving overall performance. Below, we outline several optimal practices to keep your tractor’s hydraulic system running smoothly and efficiently.
4.1 Avoid Overloading
One of the most common causes of hydraulic system stress is overloading. Whether it’s a tractor being pushed beyond its weight limit or hydraulic implements being used improperly, overloading can lead to excessive pressure on the system, causing components to wear prematurely or fail entirely.
Action Steps:
Review your tractor’s hydraulic capacity before using any new attachment.
Keep a log of load limits for all hydraulic implements, and adjust operations to stay within those limits.
4.2 Proper Warm-Up Procedures
Hydraulic systems, like any complex mechanical system, require time to warm up before they are subjected to heavy work. Starting up a tractor and immediately putting it under load can cause excessive stress on hydraulic components, leading to potential damage and a decrease in system life.
Action Steps:
Let the hydraulic system idle for 5–10 minutes before engaging heavy implements.
Check the hydraulic fluid temperature before starting demanding tasks to ensure the system is fully warmed up.
4.3 Minimize Excessive Idling
Excessive idling is often a routine part of farming operations but can have a detrimental impact on hydraulic systems over time. When the tractor is idling for extended periods, it can lead to unnecessary stress on the hydraulic system and degrade the fluid’s condition.
Action Steps:
Avoid prolonged idling when the tractor is not in active use.
If idling is necessary, try to limit it to as short a duration as possible. When idle, consider turning off the engine if the break lasts longer than a few minutes.
4.4 General Tips for Reducing Hydraulic System Stress
In addition to the above practices, several general habits can help reduce stress on hydraulic systems and keep them performing at their best:
Monitor Hydraulic Fluid Quality: Regularly check the fluid level, condition, and cleanliness. Fluid that is dirty, low, or of the wrong type can cause significant damage to the system. Regular fluid changes are crucial for maintaining hydraulic system health.
Use the Right Fluid: Ensure that the hydraulic fluid used in your tractor is the right type for the climate, operating conditions, and the tractor’s specifications. Using incorrect fluids can cause clogging, poor performance, and increased wear.
Perform Routine Inspections: Regularly inspect the hydraulic system for leaks, damaged hoses, or loose connections. Early detection of minor issues can prevent more significant damage in the future.
Action Steps:
Perform regular fluid checks and top up or change the hydraulic fluid as required.
Always use the manufacturer-recommended hydraulic fluid and avoid mixing different types.
Incorporate routine hydraulic system inspections into your regular maintenance schedule.
5. Case Studies: Real-Life Examples of Hydraulic System Maintenance Success
Case Study 1: Improved Longevity Through Regular Fluid Checks
A North American farm faced frequent hydraulic system failures due to contamination and the lack of regular fluid maintenance. The farm’s hydraulic systems, used for various attachments such as plows and harvesters, were experiencing a high rate of wear and tear, causing significant downtime during peak farming seasons. The solution was simple but impactful—implementing a strict hydraulic fluid check and replacement schedule.
The Solution:
The farm invested in high-quality hydraulic fluids and ensured that fluid changes were carried out at regular intervals, in line with the manufacturer’s recommendations.
A specialized monitoring tool was used to check fluid contamination levels and fluid pressure, ensuring that the hydraulic fluid remained clean and efficient.
Results:
The farm reported a 30% reduction in hydraulic system failures after the implementation of regular fluid checks.
The lifespan of the hydraulic components was extended, saving the farm significant repair and replacement costs.
Overall operational downtime decreased by 20%, and the farm’s productivity saw an increase during critical planting and harvesting periods.
Case Study 2: Preventing Overheating with Proper Ventilation
A Middle Eastern farm faced persistent issues with overheating hydraulic systems. Due to the extreme heat in the region, the hydraulic systems on several tractors and farm implements were often overheating, leading to costly downtime and a risk of long-term damage to essential components.
The Solution:
The farm worked withMINNUO’s engineers to design a customized ventilation system for its tractors. This included the installation of enhanced cooling fans and larger radiators to ensure that the hydraulic system would remain within optimal temperature ranges, even during the hottest months.
They also improved airflow around the hydraulic reservoirs and implemented automatic shutdown features that engaged when temperatures exceeded safe thresholds.
Results:
After implementing the cooling solution, the farm experienced a 40% reduction in overheating issues.
The hydraulic systems maintained optimal fluid viscosity, improving efficiency and preventing unnecessary wear and tear on pumps and motors.
Maintenance costs were reduced by 25% as the need for major repairs due to overheating was minimized.
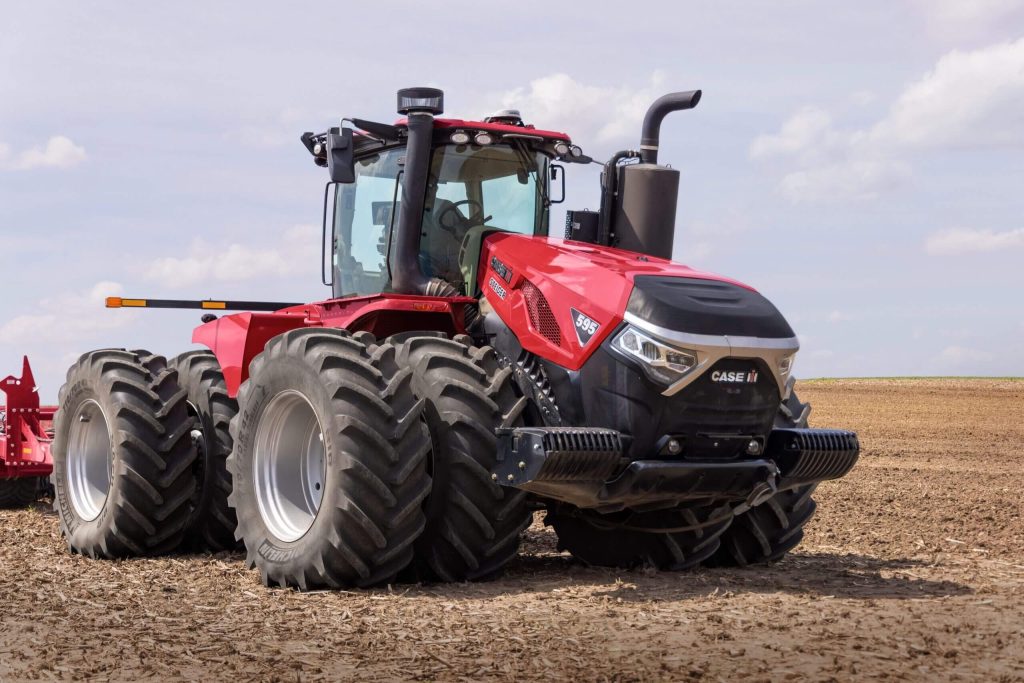
FAQ
How often should I check my tractor’s hydraulic fluid?
It is recommended to check your tractor’s hydraulic fluid at least every 100-150 hours of operation. However, if you’re working in dusty or extreme conditions, more frequent checks are advised to ensure optimal performance and prevent contamination.
What are the signs that my hydraulic system is underperforming?
Signs of underperformance include sluggish or unresponsive hydraulic functions, unusual noises like whining or grinding, overheating of the system, fluid leaks, and decreased efficiency in lifting or operating attachments. These can indicate issues such as low fluid levels, contamination, or component wear.
Can using a different brand of hydraulic fluid damage my system?
Yes, using a different brand of hydraulic fluid, especially one not recommended by the tractor manufacturer, can cause damage. It may not meet the required viscosity, lubrication properties, or additive package, leading to potential wear, overheating, or reduced efficiency of the hydraulic system.
How can MINNUO help with predictive maintenance for hydraulic systems?
MINNUO offers advanced remote diagnostics that continuously monitors your hydraulic system’s performance. By analyzing real-time data such as pressure, fluid levels, and temperature, it provides early warnings about potential issues, allowing you to address them proactively and avoid costly downtime. This predictive maintenance approach helps extend the lifespan of the hydraulic system and ensures optimal performance.
Conclusion: Prioritize Maintenance to Protect Your Investment
To maximize the lifespan of your tractor’s hydraulic system, regular checks and maintenance are crucial. By using the right hydraulic fluid, performing timely fluid changes, and leveraging technological solutions like remote diagnostics, you can prevent costly hydraulic failures and keep your tractor running efficiently.
Encouraging proactive care and taking a strategic approach to maintenance will not only minimize costly repairs but also help farmers get the most out of their equipment investment. By staying ahead of potential issues, you ensure continuous and productive operations in the field.
MINNUO’s comprehensive solutions offer long-term benefits for your tractor’s hydraulic system. With high-quality hydraulic components, tailored maintenance kits, and a robust remote diagnostics system, MINNUO helps farmers maintain their equipment at peak performance, reducing downtime and extending the lifespan of critical systems. Choose MINNUO to protect your investment and keep your hydraulic system in top condition.