In today’s agricultural economy, integrated corn threshing and drying machines have become indispensable tools in streamlining post-harvest processes. This article explores how these machines support the broader farm machinery supply chain—from the field to final packaging—by improving efficiency, reducing waste, and maximizing value. We’ll also focus on practical strategies to minimize mechanical losses during reprocessing, which is a critical challenge in the grain production industry.
So, what makes integrated corn threshing and drying equipment so valuable? The answer lies in their ability to combine multiple post-harvest tasks—shelling, separating, drying, and sometimes even cleaning—into one continuous workflow. This reduces grain handling time, minimizes exposure to moisture and contaminants, and ensures a more uniform drying outcome. However, despite their benefits, these machines can also suffer from reprocessing losses due to poor maintenance, incorrect settings, or suboptimal field conditions.
Interested in how modern engineering and agricultural technology come together to reduce waste and enhance productivity? Curious about how choosing the right equipment, settings, and servicing routines can significantly impact your bottom line? Read on for a detailed, point-by-point analysis of how integrated machines are revolutionizing the corn value chain.
Contents
- 1 From Field to Bin: The Power of Integration
- 2 Practical Friction: Where Losses Still Happen
- 3 Engineering for Efficiency: Smarter Hardware Design
- 4 The Human Factor: Operator Influence on Results
- 5 It’s All About Timing: Harvest Conditions Matter
- 6 Smart Tech Integration: More Than Just Buzzwords
- 7 Return on Investment: The Numbers Speak
- 8 Building Sustainable Operations
- 9 Conclusion
From Field to Bin: The Power of Integration
One of the greatest strengths of integrated corn processing machines lies in their ability to unify multiple steps—threshing, separation, drying, and often cleaning—into a single, continuous operation. Traditionally, these steps required separate machines and manual handling in between, which not only consumed more labor and time but introduced risks such as moisture exposure, contamination, and grain breakage.
With a well-designed integrated system, corn goes straight from the field into processing with minimal handling and faster throughput, meaning lower microbial risk and better retention of grain integrity. This seamless operation also helps farmers respond quickly to unpredictable weather, harvesting and drying corn more efficiently before sudden rainfall compromises grain quality.
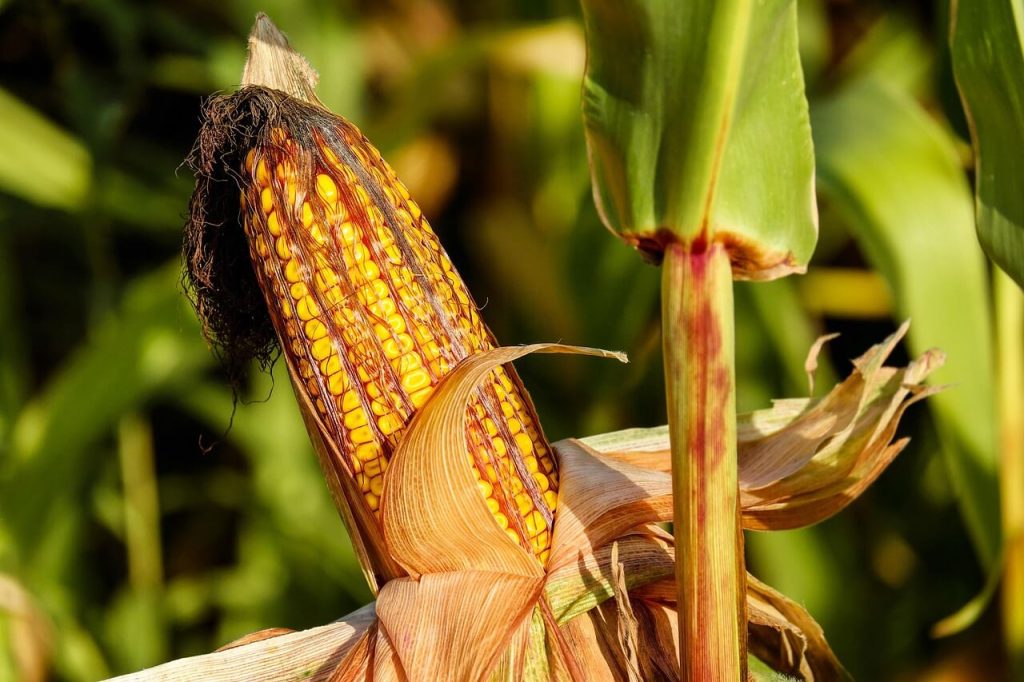
Practical Friction: Where Losses Still Happen
Despite the promise of integration, farmers still report challenges. Reprocessing losses—where shelled corn must be re-handled or corrected—remain a serious concern. These typically stem from:
- Inconsistent drum speed or feed rate, which can crack or partially shell the kernels.
- Poorly managed drying temperatures, resulting in under-dried grain prone to spoilage, or over-dried kernels that crack during storage.
- Clogged or worn-out sieves, which allow broken kernels and husk debris to mix with good grain.
- Machine overloading, which reduces the efficiency of separation and drying units and accelerates mechanical wear.
The impact? Lower market grade, increased spoilage risk, and reprocessing costs that can eat into already thin profit margins.
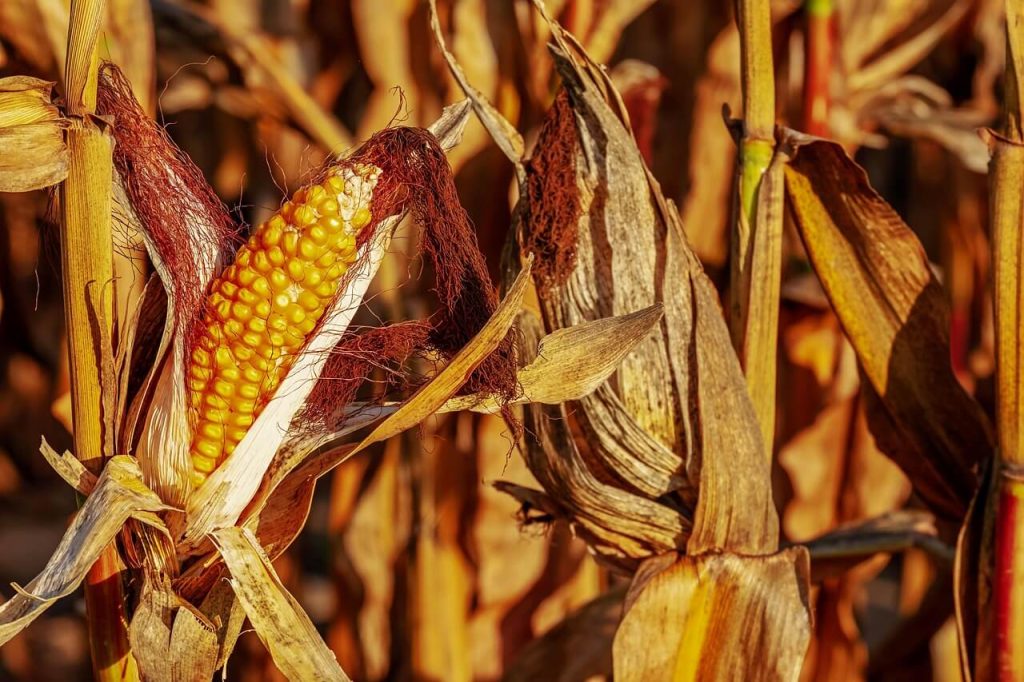
Engineering for Efficiency: Smarter Hardware Design
Modern machines are now built with adjustable mechanical parameters and intelligent sensing systems that help reduce manual guesswork. For example:
- Variable drum speeds and feed rollers allow the machine to be tailored to different moisture levels and kernel types.
- Digital temperature and humidity sensors maintain precise drying conditions and alert operators to deviations in real time.
- Sealed internal transfer paths, such as enclosed augers and smooth-surface hoppers, reduce contamination and minimize kernel damage during movement.
These design improvements offer more than convenience—they represent real cost savings by preventing avoidable grain losses and extending the lifespan of the machine through reduced strain.
The Human Factor: Operator Influence on Results
Technology aside, operator behavior plays a critical role. Many issues occur not because the machine is flawed, but because it is misused. Here’s what makes the difference:
- Regular calibration ensures that output matches the intended moisture levels and separation quality.
- Daily maintenance routines, like cleaning out dust from air ducts or inspecting belts for wear, can prevent costly failures mid-harvest.
- Operator training is often overlooked but can drastically reduce human error. Understanding machine settings, crop behavior under different field conditions, and troubleshooting alerts ensures smooth operation.
For cooperatives or multi-user machines, standardizing training across staff helps reduce inconsistencies and keeps operational standards high.
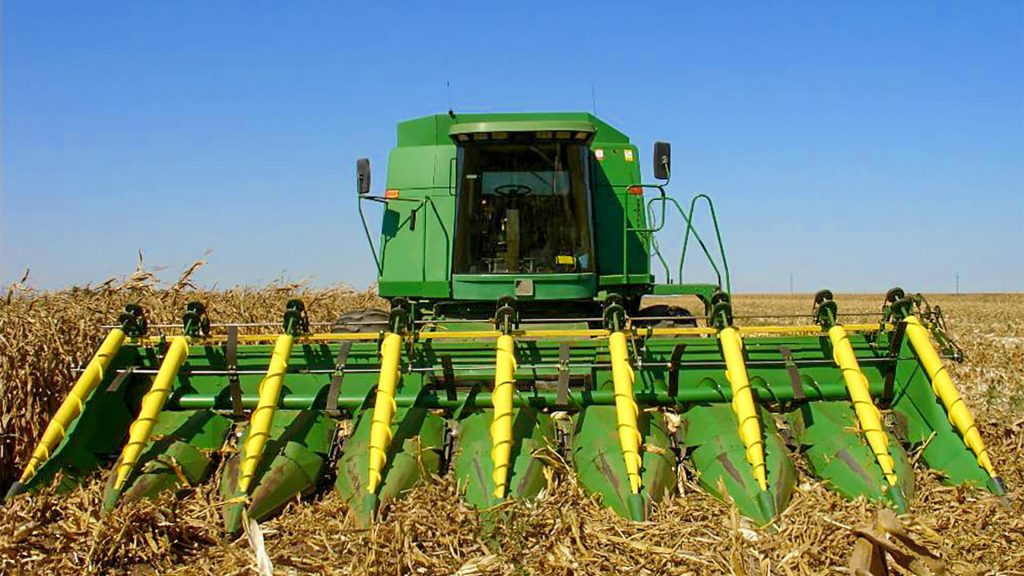
It’s All About Timing: Harvest Conditions Matter
Even the best machines can underperform if deployed under the wrong conditions. A few best practices:
- Harvest when grain moisture is around 20–25%, allowing for efficient threshing without needing overly aggressive drying that damages kernels.
- Avoid harvesting in soggy or muddy fields, which causes mud buildup inside the machine and increases maintenance downtime.
- Plan harvest schedules in blocks to keep machines working within their ideal throughput range, minimizing idle time and overload cycles.
Some farmers make the mistake of running machines at full load constantly, thinking it’s more efficient—but in practice, this wears down components faster and increases the chances of blockages or drying inconsistencies.
Smart Tech Integration: More Than Just Buzzwords
The digital transformation of agriculture isn’t coming—it’s already here. Integrated corn machines are increasingly equipped with:
- IoT sensors that track moisture, grain flow, and temperature in real time.
- Cloud-based analytics dashboards that log performance and highlight efficiency drops or abnormal trends.
- Telematics systems that help coordinate maintenance, spare part ordering, and even operator scheduling.
This kind of data-backed decision making empowers farms to move from reactive to preventive management, reducing emergency repairs and unexpected downtime.
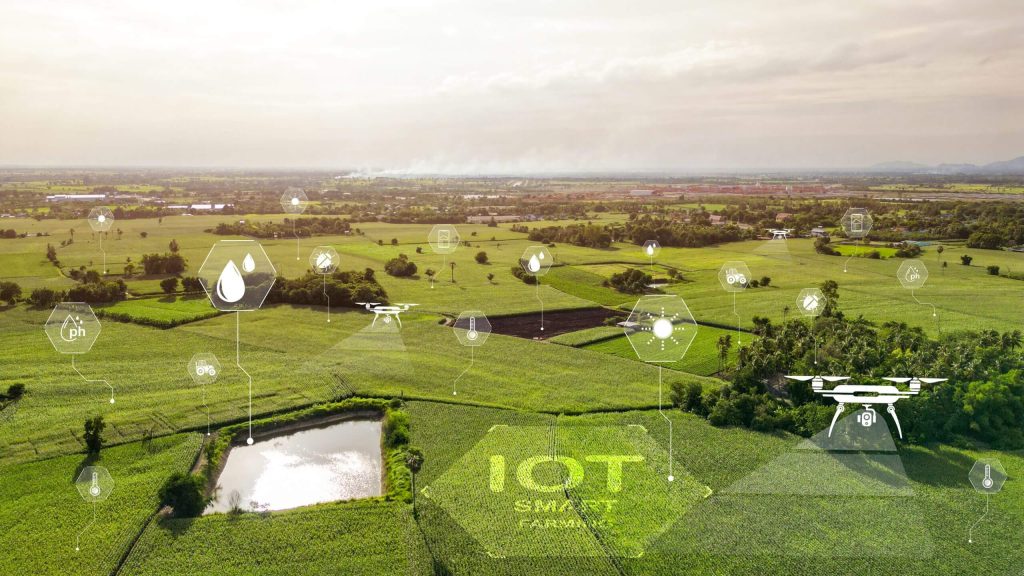
Return on Investment: The Numbers Speak
Yes, integrated machines are a significant investment. But the ROI is compelling when you consider:
- Lower labor dependency—one operator can now do the job of three.
- Improved grain uniformity, leading to better prices and fewer downgrades from buyers.
- Reduced post-harvest loss, which in some documented cases has improved saleable yield by 10–15%.
One farm in Argentina that transitioned to integrated processing systems reported a 25% drop in drying fuel costs and a 12% bump in grain accepted by buyers without additional cleaning or re-drying.
Building Sustainable Operations
Environmental responsibility is now part of economic sustainability. Integrated machines help reduce:
- Fuel consumption by consolidating processes into one engine cycle.
- Grain loss, which directly reduces the carbon footprint per kilogram of corn produced.
- Air and dust pollution, thanks to sealed systems and smart exhaust controls.
As governments and buyers place more emphasis on climate-smart farming, these machines are positioning farms for future incentives, compliance, and market access.
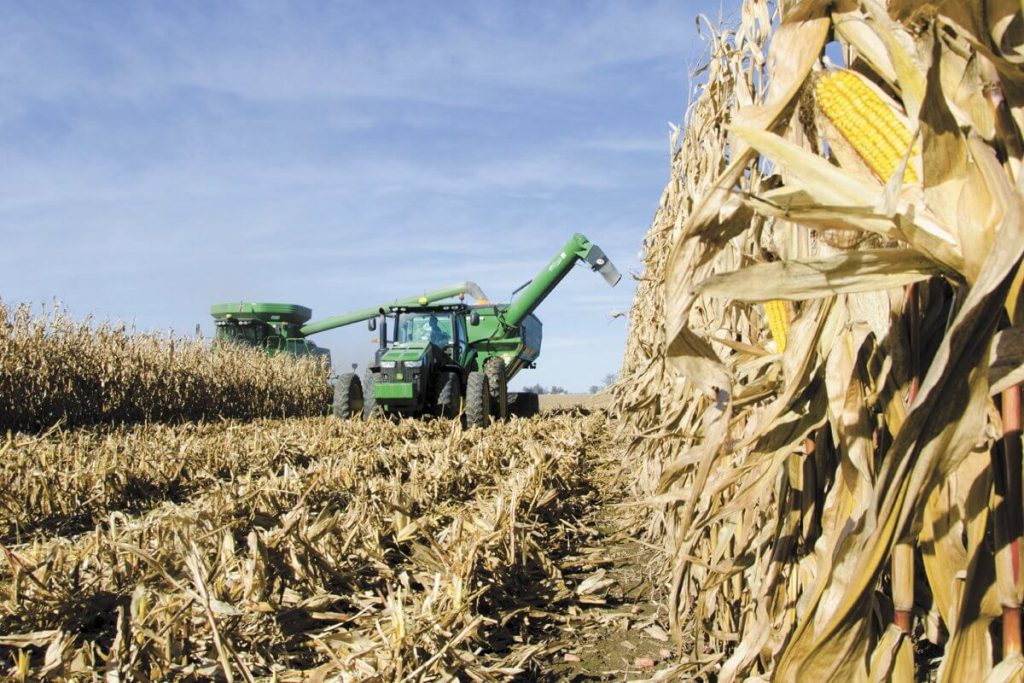
Integrated corn threshing and drying machines are more than a trend—they’re a foundational shift in how farms handle post-harvest processes. By cutting down on handling, improving drying accuracy, and enabling smart monitoring, they offer a full-package solution that addresses both efficiency and quality in one go.
Still, these machines aren’t magic. Their performance hinges on informed use, proper setup, and a clear understanding of how field conditions and operator habits interact with technology. That’s where ongoing support from experienced manufacturers and service partners becomes invaluable.
At MINNUO, we specialize in offering tailored post-harvest machinery solutions backed by hands-on support and expert guidance. Whether you’re looking to reduce grain loss, optimize throughput, or transition to smart farming, we’re here to help you get the most out of every harvest.
Conclusion
Integrated corn threshing and drying machines play a transformative role in modern agriculture, bringing efficiency and consistency to the post-harvest process. By understanding the causes of reprocessing loss and applying targeted solutions, farmers can protect yield quality and ensure better returns.
For farms seeking reliable, precision-engineered solutions, MINNUO’s agricultural machinery services offer tailored equipment and expert support designed to minimize waste and enhance productivity throughout the crop cycle. As agriculture continues to evolve, MINNUO remains a trusted partner for forward-thinking farmers worldwide.