In the selection of agricultural machinery, many farmers have the misconception that “the bigger the equipment, the better, and the higher the horsepower, the less likely to break down”. However, the actual operation shows that the applicability of the harvester is not only linked to the price, but also closely related to the scale of operation, plot structure, crop types. Whether it is 5 acres of self-cultivated fields, or 500 acres of rotational cropland, different users in the performance needs and investment capacity show significant differences.
Therefore, “selecting a machine according to needs” is the core principle of scientific selection. Choose a harvester that can meet the actual operational needs of the farm, but also in terms of efficiency, fuel consumption, failure rate and other aspects of the balance of the harvester, often than “buy big and buy expensive” to bring higher economic benefits. Especially in the price of harvester, late maintenance costs continue to rise, how to avoid overspill and waste of resources, most farmers become the most concerned about the problem.
In this article, we will compare the different logics of small and large farms in choosing harvesters from multiple dimensions, such as operating area, terrain adaptability, power configuration, return on investment, and intelligent trend, and provide a set of grounded and replicable selection suggestions combined with MINNUO’s actual product solutions, so as to help farmers of different scales to accurately choose and rationally purchase harvesters.
Contents
- 1 I. Farm size determines the logic of selection: operating area and terrain are key
- 2 II. Comparison of harvester core parameters: from “just need” to “overmatching”
- 3 III. Cost analysis: one-time investment ≠ total cost
- 4 IV. Match between crop and operation cycle
- 5 V. Significance of Smart Trends for Different Users
- 6 VI. Suggestions for practical selection: Inferring product configuration from usage scenarios
- 7 Conclusion
I. Farm size determines the logic of selection: operating area and terrain are key
When choosing a harvester, first of all, a basic principle needs to be clarified – “not blindly pursuing the big, but pursuing the right”. The size of the farm, the terrain, the distribution of land plots, and the financial ability directly determine the practical value of the harvester and the return on investment.
1. Logic of selection for small farms
Basic characteristics:
Limited area and scattered plots: most of them are within 3-30 acres, and may be separated by ditches, ridges, and roads, with little space for turning.
Complicated operating environment: there may be steep slopes, wetlands, bumpy plots and other special environments, which require high equipment passability.
Low intensity but variable frequency of operation: family labor is the mainstay, and there is a greater demand for “lightweight and high-frequency” type equipment.
Limited capital budget: the capital for purchasing machines is concentrated in the range of 50,000-150,000 RMB, and they are more inclined to “short-term results and low failure rate” equipment.
Suggestions:
Priority should be given to small self-propelled or trailer harvesters with a cutting width of 1.2-2.2m;
Support the interchangeability of multi-purpose modules (e.g., rice and wheat harvesting);
Low fuel consumption, low maintenance costs, and suitable for one-person operation;
Equipped with simple electronic control systems, not strongly dependent on intelligent platforms.
2. Logic of selection for large-scale farms
Basic features:
Continuous planting, large operation scale: the area of a single field is more than 100 acres, which is suitable for efficient operation of large-sized straight-line machinery;
Urgent operation window: the planting and harvesting seasons are clear, and the requirement of one day’s operation area is high, with a strong timeliness;
High performance requirements for equipment: the equipment needs to operate continuously for a long period of time and under high loads, and the ratio of reliability to fuel consumption has become the core index;
Intelligent operation conditions: There are conditions for deploying remote scheduling system for full-cycle operation data analysis and optimization.
Suggestions for selection:
Priority is given to efficient self-propelled harvesters with a cutting width of more than 3.5m and a level of more than 100 hp;
support GPS/RTK navigation, remote diagnosis of faults, and visualization of operation management platforms;
equipped with comfort-enhancing configurations such as electronically-controlled hydraulic systems and air-conditioned cockpits.
Farm Size | Recommended harvester features | Selection focus |
Small (<30 acres) | Compact and lightweight, low fuel consumption, removable modules | High flexibility, cost-effectiveness, ease of maintenance |
Medium (30-100 acres) | General-purpose, multifunctional machine with moderate intelligence | Performance and cost balance, scalability |
Large (>100 acres) | High horsepower, auto-guidance, all-weather high loads | Operational efficiency, data linkage, reliability |
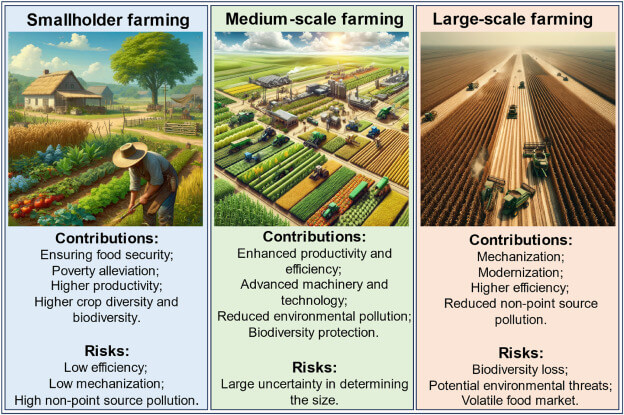
II. Comparison of harvester core parameters: from “just need” to “overmatching”
Farms of different sizes have very different needs for harvester core parameters. Small farms focus on “just enough”, emphasizing flexibility and low operating costs, while large farms need “enough and enough” to ensure efficiency and reliability under high-intensity operations. Comparing the following six parameters, we can see the logic of the transition from “just enough” to “overmatching”:
1. Cutting width
Small farms: generally choose a cutting width of 1.2m-2.5m, which is suitable for frequent turnarounds between narrow ridges and small plots of land. Small farms: generally choose 1.2m-2.5m cutting width, suitable for narrow ridges and small plots.
Large farms: more than 3.5m-6m wide cutting width models to reduce the number of walking back to improve the single hour harvesting area.
✅ Tips: The larger the cutting width, the better, should take into account the shape of the plot and turning space.
2. Power matching
Small models: mostly 25-60 hp, to meet the basic operational needs, low fuel consumption.
Large model: equipped with more than 100 horsepower engine, some support dual drive or hybrid, suitable for continuous heavy load operation.
✅ Tip: Horsepower redundancy will cause fuel waste, and it is recommended to match the power according to crop type and terrain gradient.
3. Operational efficiency
Small harvesters: pursue lightweight and high-frequency attendance, suitable for flexible scheduling and multi-scenario switching.
Large harvester: Focusing on production capacity per unit of time, adopting high-strength conveying and fast threshing system, and realizing “mu yield hour harvesting” in high-density maturity period.
✅ Tip: You can refer to the crop “maturity window period” + “target operating area” to evaluate the reasonable daily operating volume. 4.
4. Adaptability to terrain
Small equipment: more friendly to ridges, corners and broken plots, and quick access to narrow areas.
Large-sized equipment: more suitable for large pieces of farmland, high-speed linear plots, with higher requirements for access space.
✅ Tip: When the plot is separated by forest belt, water channel or road, small or modular equipment combination is preferred.
5. Transit ability
Small models: foldable, simple hitch towing ability, suitable for multi-plot crop rotation scenarios.
Large-scale models: often need to use pallet transportation, not suitable for frequent transfer, high transportation costs.
✅ Tip: It is recommended to use the “cost of transshipment to the furthest field” as a criterion for evaluating the economics of transshipment.
6. Maintenance and spare parts
Small harvesters: simple structure, easy maintenance, low cost and quick replacement of wearing parts (e.g. screens, threshing tines).
Large harvester: complex structure, mostly customized modules, high requirements for skilled workers’ operation and fault judgment ability.
✅ Tips: MINNUO supports remote module diagnostic function and APP spare parts number query, which is convenient for farmers’ self-inspection and quick procurement.
Parameter Dimension | Small farm harvester | Large farm harvesters | Recommended adaptation scenarios |
Cutting Width | 1.2m-2.5m | 3.5m-6m+ | Small field/hilly land vs. continuous flat land |
Power Configuration | 25-60hp | ≥100hp | Low to medium intensity operation vs. continuous heavy duty operation |
Operational Efficiency | Flexible HF | Powerful and efficient | Fragmented management vs. targeted maturity |
Turning Capacity | Easy to load and haul | Heavy truck transfer | Multi-farm rotation vs. integrated and continuous farmland |
O&M Costs | Easy to source accessories | Specialized service | Self-maintenance vs. vendor support |
III. Cost analysis: one-time investment ≠ total cost
Many farmers tend to fall into the misunderstanding that “price is king” when purchasing a harvester, believing that cheapness means saving money. However, in the life cycle of agricultural machinery, the “one-time investment” is only the beginning, and the bigger expenses often come from the subsequent use and maintenance. Therefore, whether it is a small farm or a large planting base, a scientific assessment of the Total Cost of Ownership (TCO) is the basis for more informed decision-making.
1. Purchase Cost ≠ Unique Cost
Farm type | Reference budget for adapted harvester | Features |
Small farms | ¥50,000-¥150,000 | Optional tractor + hitch type harvesting module, flexible transfer, low investment threshold |
Large farms | ¥150,000-¥800,000+ | All-in-one or high-horsepower, high-cutting-width model with automated control system, large investment but high efficiency per acre |
✅ Tips: small farms are recommended to keep the budget within 100,000 yuan, and set aside 1-20,000 yuan for initial modification or module expansion; large farms can be based on the average acre budget (such as acres/total price of the equipment <300 yuan) to reverse the reasonable purchase level.
2. Utilization cost: Hidden expenses should not be ignored
In addition to the purchase cost of the machine, the utilization cost incurred in the annual operation is the key to affect the revenue:
Type of cost | Details | Control recommendations |
Fuel/electricity | Fuel consumption per hour 3-6L, motor unit about 1.2-2kWh/h | Prioritize energy-saving electronically controlled harvesters (e.g., MINNUO’s new fuel-saving system) |
Labor costs | Driver 1-2 persons/table, some high-level models can be dispatched by one person for more than one machine | Reduce repetitive operations by installing automated pathfinding modules as much as possible |
Maintenance frequency | Replacement of spare parts (blades, screens, drive shafts, etc.), quarterly or every 500h inspection | Purchase models with simplified maintenance structures, and recommend the use of equipment with a self-checking system for malfunctions |
Depreciation costs | High depreciation of large-sized equipment after 3-5 years. High depreciation after 3-5 years for large equipment, but flexible for small equipment. | Smaller equipment is easier to transfer or lease for recycling, and platformized models with a “higher residual second-hand value” can be selected |
✅ Practical example: a small 60 hp harvester costs about ¥8,000 per year in fuel consumption + maintenance, while a large 200 hp harvester may cost ¥25,000-¥30,000 for a single round of maintenance.
3. Payback cycle: varies by farm size and crop season
Type | Payback method | Recycling cycle reference |
Small farms | Stabilized use + cost compression“ to achieve marginally profitable operation | Approx. 2-4 years |
Large farms | Amortization of costs through ”large-scale operation + multi-season crop rotation” | Approx. 1-3 years |
Trustee cooperatives | Multi-location transfer service with high revenue flexibility | Recyclable cycle < 2 years |
✅ Calculation suggestion: Divide “equipment depreciation + annual cost of use” by “workable acres × cost savings or yield gains per acre” to determine whether the payback cycle is reasonable.
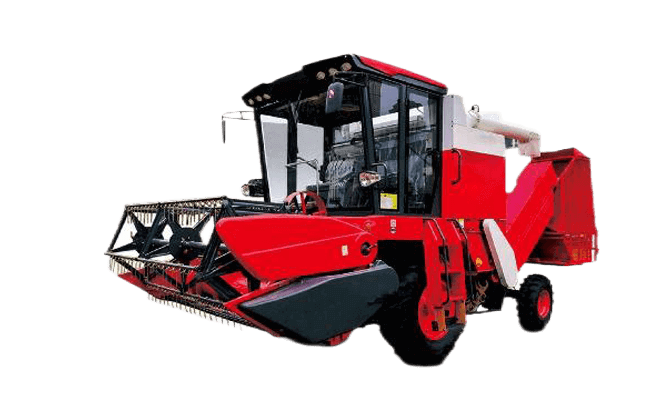
IV. Match between crop and operation cycle
Crop type, maturity and sowing/harvesting rhythm directly determine the operation time window and suitability of the harvester. Harvester is not a “one-size-fits-all machine”, different types of equipment in the face of a single crop harvesting or a variety of crops in rotation, its efficiency, structural configuration and economy there are significant differences. Therefore, at the selection stage, it is necessary to consider the suitability of the main local crop types and operating cycles.
1. Requirements for harvesting structures vary considerably from crop to crop.
Crop Types | Operational Difficulty | Requirements for harvester configuration |
Rice, wheat (granular) | Harvesting efficiency at the core | Adjustable cutting height, high threshing efficiency, low grain loss |
Corn (separated ears and stems) | Robust crop | Strong threshing power + peeling + straw crushing device required |
Soybeans (fall-over fragile) | Prone to cracking pods and dropping kernels | Low cutting + flexible drum + anti-mess design required |
Oilseed rape (concentrated maturity) | Uneven maturity | Precise harvesting height adjustment with windrower required |
Vegetables (e.g., kale) | Needs to be harvested as a whole plant | Adaptable clamping + conveyor belt + low-damage knife set design |
✅ Extended recommendation: if the farmer is mainly a grain farmer, he can choose a general-purpose grain harvester; if he grows a variety of crops (e.g. corn + soybean + green storage), he is recommended to choose a multi-purpose harvesting platform (e.g. MINNUO series) with interchangeable cutting deck modules. 2.
2. The operating cycle determines the “reaction speed” of the equipment.
Different crops have different concentrations of maturity, which requires the equipment to complete the task within a limited window to avoid yield loss:
Crop Maturity Window | Small harvester suitability | Suitability of large harvesters |
Centralized harvesting (e.g., rice, corn) | Easily staggered, need to rationalize scheduling | Highly efficient bursts, suitable for large-scale one-week completion |
Asynchronous maturation (e.g., oilseed rape, soybeans) | Can be phased in regionally | Need to set up “staged routes” to reduce idling |
Multi-batch harvesting (vegetables, green manure) | Smaller equipment can follow flexibly | Large machines need to be used in conjunction with a turnaround logistics system |
✅ Tips: When the harvesting window is less than 5-7 days, operational efficiency is the key, and we recommend using ≥3.5m wide cutting decks and ≥100 hp high-speed harvesters; on the contrary, if the plots of land are scattered or the harvesting rhythm is decentralized, we recommend the low-horsepower flexible equipment. 3. Multi-crop + rotational farms: Prioritize module expansion capability
3. Multi-crop + rotational farms: give priority to module expansion capability
For medium and large-scale farms with frequent replanting, it is recommended to choose a modular model with functions such as “cutting deck interchangeability + windrow/conveyor + green storage/threshing switching”, which can realize:
intra-seasonal switching (e.g., harvesting oilseed rape in the spring → soybeans in the fall);
diversified uses (supporting grains + tubers at the same time); rapid cutting deck interchangeability (e.g., harvesting oilseed rape in the spring → soybeans in the fall); and fast cutting deck interchangeability (supporting grain + tubers). Diversified uses (supporting grains + tubers at the same time);
quick interchange of cutting tables (change within half an hour);
adjustment of discharge paths (sorting in the direction of seeds/whole plants/straws);
support for unmanned navigation path multiplexing (to improve the efficiency of utilization of rounds).
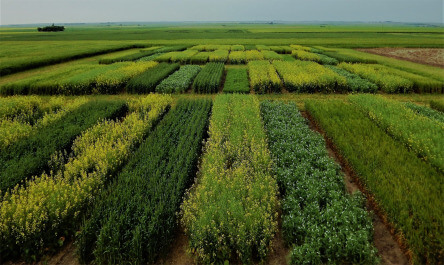
V. Significance of Smart Trends for Different Users
The popularization of smart agricultural technology is not one-size-fits-all, but should be promoted in layers and precisely adapted according to differences in user size, technical ability, planting density and operational intensity. For different types of farmers, “intelligent” is not just buying equipment, but also a change in the concept of farm management. 1.
1. Small farms: lightweight intelligence, improve operational fault tolerance
Small farms are mostly family-run or decentralized contracting, with limited labor and scattered plots of land, and the goal of intelligence is to be “affordable, understandable, and quick to operate”.
✅ Recommended function direction:
Function type | Recommended Description |
GPS auto navigation assisted driving | Precise straight line driving, suitable for novices, reduce physical exertion and wrong line |
Map track recording + auto acreage counting | Used to check the harvesting and sowing coverage, convenient for fine reconciliation and replanting |
One-touch path return, fixed-point auto turn | Enhance the turning efficiency in small fields, reduce the omission of replanting |
Basic agricultural condition recording module | Manually record the time of fertilizer application and spraying, to form a simple “agricultural logbook”. |
✅ Operational advantages:
Reduce the probability of misoperation and save manpower;
Do not rely on complex peripherals, retaining the flexibility of manual intervention;
Large space for upgrading in the future, avoiding the burden of “expensive configuration at the beginning”.
✅ Equipment Suggestion:
can choose the MINNUO light intelligent navigation system, which supports the standard tablet control interface, and is suitable for medium horsepower harvester, rice transplanter and cultivator, which is quick to start and simple to maintain. 2.
2. Large-scale farms/cooperatives: comprehensive digitization to improve collaborative efficiency
The biggest challenge faced by large-scale farms is “collaborative efficiency” and “unified and standardized management”, which requires highly integrated remote control and data platform capabilities.
✅ Recommended System Architecture:
Module | Functions and Roles |
RTK+unmanned system | Enhance sowing and harvesting precision, reduce manual errors and waste of man-hours |
Cloud data scheduling platform | Split-unit operation plan issuance, path planning, man-hours statistics |
Real-time monitoring system of agricultural machinery operation images | Combine cameras and sensors to remotely monitor driving trajectory, turning accuracy, and preventing leakage of harvesting |
Agricultural situation AI recognition system | Cooperate with the overhead camera of drones or tractors to automatically identify pests and disease and seedling abnormality |
✅ Typical Configuration:
Driverless tractor + intelligent terminal + cloud platform scheduling APP
Support “multi-machine cooperation” “map pointing” “operation statistics” “operation abnormal alarm” ✅ Management Value: Reduce the cost of multi-point coordination; realize remote centralized management; support multi-batch operation unified statistics, report generation. “Abnormal operation alarm”
✅ Management value:
Reduce the cost of multi-point coordination;
Realize remote centralized management;
Support unified statistics and report generation for multiple batches of operations.
Scenario Comparison and Intelligent Deployment Suggestions
Farm size type | Intelligent Key Functions | Recommended configuration combinations |
Small family farm | GPS Navigation + Acreage Counting + Track Recording | MINNUO Light Navigation Module + Visualization Tablet Operation |
Medium-sized rotational farm | Multi-Crop Track Overlay + Path Planning | MINNUO Data Management Platform + RTK Module |
Large cooperative | Cloud Platform Unified Scheduling + Job Collaboration + Image Recognition | MINNUO Full Stack Intelligent Control System + Remote Collaboration Component |
VI. Suggestions for practical selection: Inferring product configuration from usage scenarios
Purchasing a harvester is not “the bigger the better” or “the stronger the performance the more advanced”, but rather, it should be based on a comprehensive assessment of the actual situation of the farm, the crop structure and the intensity of the operation, and the selection of the model should be based on the scenarios in order to realize the optimal cost and maximize the efficiency of use. To achieve the optimal cost and maximize the efficiency of use.
✅ Scenario 1: 10 acres or less (self-planting + part-time)
Typical user characteristics: family planting, small-scale contracting, low frequency of harvesting, but the need for flexible transfer.
Characteristics of recommended models:
1.2m~1.5m cutting width;
tractor-driven or self-propelled structure;
easy operation, low maintenance costs;
easy to turn, easy to get on and off the trailer, suitable for fragmented plots or hilly areas.
Recommended products:
MINNUO 1.5m Hopping Harvester
Harvesting/threshing in one machine, suitable for 20~35 hp tractor;
Simple mechanical structure, easy to maintain;
Daily operating capacity of about 1~2mu, suitable for self-use+emergency plowing.
✅ Suggestions:
We suggest configuring simple tension chain and diesel fuel saving device;
Optional manual height adjustment device to adapt to different plant heights.
✅ Use Scenario 2: 30~100 mu (family joint operation)
Typical user characteristics: Home operation is the main focus, taking into account the help of neighboring operations or harvesting services.
Recommended features:
Cutting width of 2.0m~2.5m;
Support wheat/corn/rape and other crops to change the module;
Horsepower of 50~70 horsepower to adapt to different soils;
Enhance the harvesting efficiency and reduce the time of lost labor.
Recommended products:
MINNUO Multi-purpose Harvesting Platform
Quickly change crop modules (straw/corn/beans);
Equipped with double side conveyors, suitable for hilly/sloping land;
Supports work track record and acre yield estimation.
✅ Operation Suggestion:
It is recommended to match with stubble height adjustment + terrain-adapted wheelset;
If you have more than one plot to work, it is more convenient to equip with the function of “Quick Folding Rack”.
✅ Usage Scenario 3: More than 300 acres (cooperative/operating service team)
Typical user characteristics: harvesting several times a year, serving multiple customer plots, standardized operation, low tolerance for failure.
Recommended model features:
Cutting width of 3.5~4.5m or more;
Equipped with an engine of 100 hp or more;
With intelligent control terminal, remote scheduling system and data export interface;
Supports unmanned or preset route operation.
Recommended products:
MINNUO Intelligent Dada Cooperative Work Kit
Integrated RTK navigation system, accurate harvesting of rows;
supports wireless uploading of working hours data, remote warning;
can be set up according to the crop, weather conditions, automatic operation parameters.
✅ Operation and Maintenance Suggestions:
It is recommended to equip with “remote warning system + regular maintenance reminder”;
Equipped with high efficiency threshing + residue detection system to meet the green standard.
Scenario Comparison Selection Summary Table
Use Scenarios | Cutting width range | Recommended Configuration Highlights | MINNUO Reference Models |
Up to 10 acres | 1.2~1.5m | Towable/lightweight, self-contained | 1.5m Hopper Harvester |
30 to 100 acres | 2.0~2.5m | Multi-crop module, higher power, off-hook transit | Multi-purpose Harvesting Platform |
300 acres or more | 3.5~4.5m+ | RTK navigation, intelligent control, data visualization | Intelligent Cooperative Work Kit |
Conclusion
Different types of farms face very different priorities when choosing a harvester – small farms need to be flexible, easy to operate and cost-controlled, while large farms pay more attention to high efficiency, multi-functional integration and intelligent operation. It can be seen that the selection of harvester should not pursue “buy the most expensive”, but should look for “the most suitable” – not only to match the conditions of the plot, but also to match the intensity of operation and crop structure.
MINNUO has always been committed to providing customized harvesting equipment solutions for farms of different sizes. Whether it is a lightweight model for self-planting users or an intelligent big field platform for cooperatives, MINNUO supports module expansion, remote operation and maintenance management and after-sales guarantee, helping farmers realize stable yield and efficiency, save costs and increase income, and move forward to a green, efficient and sustainable agricultural development.