In modern agricultural production, agricultural machinery has become an indispensable production tool. However, with the increase in operational intensity, the complexity of environmental conditions (e.g., high temperature and humidity, dust and sand), and the increase in the degree of equipment intelligence, the frequency of failures of agricultural machinery and equipment is also increasing year by year. Whether it is a traditional tractor or an intelligent farm machine equipped with RTK navigation and electronic control system, the risk of problems in its operation is increasing. This article is centered around the common types of farm techniques machinery failure to provide farmers with a set of systematic troubleshooting ideas.
Farm machinery failure is not terrible, the real risk is “found in a timely manner” and “maintenance costs are too high”. If you can not identify the problem in the first time, accurately determine the cause, often lead to the expansion of equipment damage, delayed farming time, maintenance costs doubled, and even triggered a chain of economic losses. Especially during the busy farming period, an hour’s delay may be the loss of yield of several acres of land. Therefore, improving the farmer’s own “diagnostic response capability” is no longer an option, but a “must” for modern agriculture.
Through this article, readers will learn how to quickly locate faults in key areas such as the engine, the electronic control system, the hydraulic module, the power and transmission unit. At the same time, will also understand how to use tools, sensors, APP and other means to achieve intelligent, autonomous operation and maintenance management of agricultural machinery. If you want to “spend less money and delay less farm time”, you may want to read on, so that “know how to repair” becomes the new competitiveness of farm operation.
Contents
- 1 Ⅰ.The engine system common failures and troubleshooting skills
- 2 Ⅱ.The hydraulic system common failure and troubleshooting skills
- 3 Ⅲ. Electronic Control System Failures and Basic Diagnostic Methods
- 4 Ⅳ.The electric power system and transmission system basic troubleshooting
- 5 Ⅴ.The establishment of agricultural machinery failure warning and maintenance system
- 5.1 1. Formulate a “phased inspection list”: set up maintenance nodes according to 100h, 500h and 1000h.
- 5.2 2. Promote digital maintenance logs: Realize closed-loop management of equipment health records
- 5.3 3. Introducing intelligent sensors + remote fault warning mechanism
- 5.4 4. Suggestions and Precautions
- 6 Conclusion
Ⅰ.The engine system common failures and troubleshooting skills
Agricultural machinery engine is the “heart” of the equipment, once the problem occurs, will directly lead to operational disruption. Therefore, to understand the typical performance of engine failure, determine the cause and treatment methods, to ensure the stable operation of agricultural machinery is of great significance.
1. Common Failure Phenomena and Possible Causes
Starting Difficulty / Unable to start:
Battery power loss, poor battery contact;
starter motor failure or brush wear;
air in the diesel fuel tank or fuel system clogging (such as fuel pump or injector nozzle clogging).
Abnormal temperature (overheating) during operation:
Lack of liquid in the tank or coolant leakage;
Stuck thermostat or deviation in opening temperature;
Fan failure due to loose or broken fan belt;
Severe accumulation of dust on the outside of the radiator, which affects air circulation.
Shuddering and unstable idling:
Ignition timing deviation or wrong injection advance angle;
Poor atomization of fuel injectors or carbon deposits;
Abnormal intake and exhaust valve clearance.
2. Suggestions for investigation and repair
(1) Electrical system inspection:
Use digital multimeter to measure the static voltage of the battery:
Standard reference value: ≥12.5V;
If it is lower than 12V, the vehicle can not be started normally in most cases;
Check whether the battery terminal is oxidized or loose.
(2) Cooling system check:
Open the hood of the engine and observe whether the water tank is short of liquid;
Check whether the water pump is leaking and whether the thermostat can open the cycle at high temperature;
Replace the fan belt with the same type of belt if it is loose or broken;
Clean the weeds, dust and sludge on the radiator.
(3) Fuel system check:
check whether the diesel filter is clogged, it is recommended to replace it once every 300 hours;
observe whether the oil return pipe is normal and whether the oil pump is smooth;
check the atomization of injector nozzles, and it should be cleaned or replaced when there is carbon scale.
(4) Air supply system check:
Disassemble the air filter element and replace it immediately if it is found to be seriously clogged;
Check whether the air intake pipe is cracked or loosely connected to prevent insufficient air intake or mixing with dust.
✅ Practical advice: use infrared thermometer to scan the water tank, cylinder, thermostat, to quickly determine the source of overheating, to avoid “misrepair”.
3. Quick troubleshooting process recommendations (sequential elimination method)
Steps | Parts to Investigate | What to check | Typical Problems |
First step | Battery and Wiring | Is the voltage up to standard, is the wire loose | Loss of battery power, faulty starter relay |
Second step | Cooling System | Is there any lack of liquid, is the water pump/fan/thermostat normal | Overheating, temperature control failure |
Third step | Fuel System | Is the diesel fuel filter, injector nozzle, fuel supply pump clogged | Stalling after starting, intermittent fuel supply |
Fourth step | Ignition/Injection System | Is there any poor atomization, inaccurate injection timing | Jitter, lack of power |
Fifth step | Air Intake System | Is the filter element clean, is the intake pipe cracked or aged? | Sucking in impurities, erratic idling |
4. Suggested list of tools (suitable for farmers to keep on hand)
Digital multimeter (to measure voltage, resistance, continuity)
Infrared thermometer (to quickly identify the source of high temperatures)
Torque wrench (to correct belt tension, tighten bolts)
Injector nozzle tester (to facilitate the determination of the state of the fuel injection)
Paper Engine Troubleshooting Comparison Chart (recommended to be affixed to the wall of the hangar)
Ⅱ.The hydraulic system common failure and troubleshooting skills
Hydraulic system in agricultural machinery plays an indispensable role, especially widely used in lifting, steering, turning, clamping and other institutions. Once the hydraulic system fails, it will not only affect the efficiency of the equipment, but also may lead to the interruption of agricultural operations. Therefore, mastering the common types of failure and troubleshooting skills is essential to extend equipment life and avoid downtime losses.
1. Common failure types and performance
Type of malfunction | Description of the performance |
Weakness in lifting/turning | The operating device cannot be lifted, the overturning speed is slow or the movement is interrupted |
Hydraulic oil leak | During the operation, the hydraulic cylinders, joints or pipelines are obviously leaking |
Increased oil temperature, slow operation | The oil becomes black, the oil temperature alarms, and the movement is obviously delayed |
Broken or poorly sealed lines | The operation is accompanied by the injection of hydraulic oil and the sudden drop of pressure |
No movement | There is no response after the startup, and the control valves/commutator do not work |
✅ Practical experience reference:
If there is “lifting stuttering + slow operation”, prioritize checking the oil temperature and whether the filter element is clogged.
2. Analysis of common causes of failure
Hydraulic pump problems:
pump gear wear, pump shaft fracture, suction filter clogging, resulting in insufficient oil suction;
hydraulic pump and motor coupling loosening, the power can not be transmitted;
oil circuit abnormalities:
pipeline rupture, joints loose, the hydraulic oil circuit is not closed;
tank level is too low, poor oil suction;
control valve failure:
multi-way valve stagnation, the main control valve spool leakage, overflow valve failure;
directional control valve does not Directional control valve does not change direction, pilot oil circuit failure;
fluid problems:
fluid has not been replaced for a long time, containing water, oxidation or emulsification;
fluid viscosity mismatch, add the unqualified hydraulic oil.
3. Troubleshooting steps and operational recommendations
(1) Detect whether the hydraulic pressure is up to standard:
hydraulic system using a special pressure gauge connected to the detection port (generally located in the pump outlet or control valve inlet), compared with the equipment manual calibration of the working pressure value (such as 18 ~ 22MPa);
if lower than the rated pressure of more than 10%, the initial determination of the pump wear or pressure control element failure.
(2) Check the status of the oil and maintenance cycle:
If the oil color is black, viscosity decreases, accompanied by a strange smell, it is recommended to replace it immediately;
clean the oil suction filter, every 500h is recommended to replace the hydraulic oil and filter element;
oil should not be mixed with different brands and different models to avoid compatibility problems leading to system disorders.
(3) Check the hose and joints:
Check whether there are oil stains, cracks, aging and other phenomena in the pipe connections;
joints can be properly tightened (pay attention to avoid over-tightening and damaging the seals);
It is recommended that the high-pressure hose assembly be replaced once a year.
(4) Diagnosis of control valve:
Tap the valve body with a hammer to check whether it is stuck;
If the multi-way valve does not respond, try to replace the solenoid valve coil or check the power supply line;
Positioning is not permitted or the cylinder moves incorrectly, check the proportional valve feedback potentiometer.
✅ Expert advice:
Hydraulic operation can be carried out before the first 2 to 3 times “no-load cycle lifting” test, to observe whether the equipment appears “abnormal noise + jitter + hysteresis” and other warning signals, is an effective means of determining the potential failure of the system.
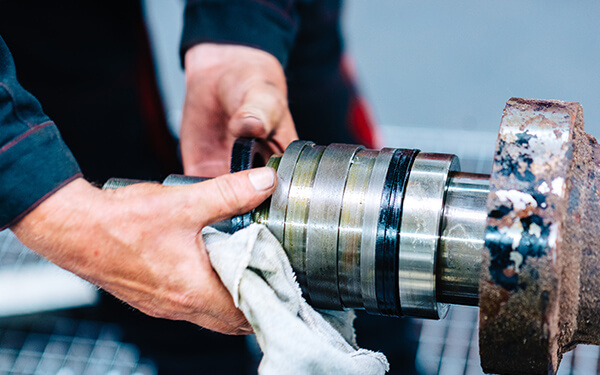
4. Daily maintenance and life extension recommendations
Inspection items | Recommended Cycle | Precautions |
Hydraulic oil quality check | Every 200 hours | Replace immediately if there is emulsification, turbidity or strange odor |
Cylinder seal check | Quarterly | Especially check the parts with frequent reciprocating action |
Pipe connection point check | Monthly | Tighten the joints to eliminate the risk of vibration loosening |
No-load test before operation | Before each operation | Lift and lower 1~2 times with no load to make sure that there is no phenomenon of “stuttering, jumping, or powerlessness”. |
Ⅲ. Electronic Control System Failures and Basic Diagnostic Methods
With the gradual intelligentization of agricultural machinery, more and more equipments are equipped with electronic control systems (ECUs), navigation modules (RTKs) and remote monitoring platforms. Although intelligence improves operational precision, it also brings new diagnosis and maintenance needs. Mastering the performance of common electronic faults and basic troubleshooting skills will help farmers quickly locate the problem, resume operations, and avoid delaying the whole machine operation due to minor faults.
1. Common electronic system problems and performance
Failure manifestation | Possible components involved | Typical Symptoms |
Instrument cluster no display / flashing | Display panel, main power supply, communication bus | No response at power on, data not refreshed, warning light blinking frequently |
GPS navigation failure / RTK interruption | Antenna, signal receiving module, control box | Map unable to locate, job track deviation, unable to navigate the job |
ECU alarm but unable to determine the position | Abnormal storage or sensors inside the electronic control unit | Abnormality code with no specific description, malfunction light is always on |
Auto steering failure | Controller, steering motor, communication interference | Unable to cut into autopilot, frequently jump out of the track |
✅ Practical reference: If the GPS signal is often interrupted, you should first check whether the antenna interface is loose, and then check whether the power supply of the RTK base station is normal.
2. Troubleshooting Methods and Basic Procedures
For troubleshooting electronic faults, it is recommended to follow the three steps of “code reading + communication + module”.
(1) Read the fault code:
Use a fault diagnostic instrument (such as OBD detector) to connect to the ECU data interface;
Read the fault code and record it, and it is recommended to take photos to save it;
Some of the MINNUO models support cell phone scanning to read the error code.
(2) Test communication and power supply:
Check whether the master control box is powered (use a multimeter to measure DC12V/24V);
Confirm whether the communication cable is detached or the connector is waterlogged;
Confirm whether the master-slave node number is the same if CAN bus equipment is installed.
(3) Component independent troubleshooting:
Remove the faulty module and insert the spare module to test whether the function is restored;
or use the same type of module to swap the test (such as navigation control box, LCD panel).
✅ Reminder: Avoid unplugging and plugging the module with electricity, it should be disconnected before replacing it to prevent short-circuiting and burning the motherboard.
3. Troubleshooting suggestions and repair ideas
Fault type | Quick Fix Suggestions |
ECU alarms but unknown codes | Press and hold the “Mode Key” to reset ECU, or restart after 3 minutes of power failure |
Autopilot stuck | Update the navigation software version + check the RTK module reception status |
Display black / dead | Unplug and re-plug the main screen connector; Replace the backlight cable |
Control box false alarms | Enter the “Software Calibration” menu to re-calibrate the control Signal |
Practical suggestions:
It is recommended to upgrade the device firmware once every 6 months;
Use MINNUO Agricultural Cloud APP to remotely read fault codes and push repair suggestions.
4. Daily maintenance recommendations and prevention
Daily Check Items | Recommended Frequency | Precautions |
Master Box Power Supply Line | Once a month | Whether the plug is loose, wiring is not water |
Display Software Update | Quarterly | Use the original APP to upgrade the version, to avoid compatibility problems |
RTK Antenna Status Check | Monthly + before each operation | The antenna position is not blocked, the cable is not broken |
ECU Diagnostics Backup | Quarterly | Use the diagnostic instrument to export the current device status, and create a file backup |
✅ Technical reminder: in the “power on no response + controller no feedback”, 90% belong to the communication or power supply problems, prioritize checking fuses, batteries, cable connections.
Ⅳ.The electric power system and transmission system basic troubleshooting
In modern agricultural machinery, the electric power system is “start + operation + intelligent control” of the energy supply core, while the transmission system is “power conduction” of the key channel. Failure of either party will affect the efficiency and stability of the whole machine. The following system is categorized according to the detailed investigation techniques and common misconceptions.
1. Power system troubleshooting
The power system mainly involves: battery, generator, starter motor, relay, wiring module, lighting system, fuse and other components.
Common symptoms and troubleshooting suggestions:
Fault manifestations | Analysis of possible causes | Troubleshooting suggestions |
Battery loss / frequent discharging | Aging battery, reduced capacity in winter, loose terminals, untimely charging | Measure the voltage with a multimeter (normal should be ≥12.5V), check the connectors for oxidization/loosening |
Generator does not generate electricity / needle does not move | Broken belt, damaged generator, faulty regulator | Check whether the generator belt is slipping or not, and whether the power generation coil is disconnected or not |
Lights do not come on / Instrument cluster does not respond | Blown fuse, damaged electronic control box, disconnected main power switch | Replace the fuses one by one → Check the connection between the master control harness and the ground |
Module malfunction (e.g., sprayer control is invalid) | Damaged control relay / moisture in control box / faulty ECU output | Open the electronic control box, and use an electric pen to test the pins of the modules to see if they are normally energized. |
✅ Practical suggestions:
The battery should be maintained regularly and replaced once a year;
Using MINNUO Smart Farming Machine is recommended to be accompanied by an intelligent power monitoring system to check the health status of the battery in real time;
The connection module must be disconnected before unplugging, to avoid burnt circuit boards due to the instantaneous voltage reversal.
2. Transmission System Troubleshooting
The transmission system includes: clutch, gear set, drive shaft, main reducer, drive chain/belt, lubrication part of the bearing shaft and so on.
Common symptoms and troubleshooting suggestions:
Failure manifestations | Analysis of possible causes | Inspection Recommendations |
Clutch slipping / pinching not disengaging | Severe wear of clutch plates, weak pressure plate spring, loss of pressure in hydraulic cylinder | Open the engine shroud and check the thickness of the clutch friction plate and the release stroke |
Difficulty in shifting / stiffness | Worn synchronizers, damaged bearings, insufficient lubrication | Check the transmission oil level and oil quality, and it is recommended to change the oil every 300 hours during the break-in period |
Wheel rim noise / idling slippage | Excessive gear meshing clearance, wear of differential teeth at wheel edges, oil seal leakage leading to dry friction | Rotate the drive wheels after lifting and observe whether there is any sense of stagnation, metal knocking sound, or sense of jerky jumping |
Significant reduction in transmission efficiency | Main drive shaft deflection, coupling detachment, loosening of fixing bolts | Check the fixing screws of the coupler and the fastening status of the bearing housings on both ends of the drive shafts. |
✅ Professional reminder:
Avoid “not changing transmission oil for a long time”, it is recommended to change the main transmission oil every 500h, and check whether there is iron powder in the oil;
Before operation, it should be “lifting and lowering with no load” for 2 times, and then enter into heavy-load operation to judge whether the response delay or vibration is abnormal;
It is recommended to use the MINNUO remote monitoring platform to visualize the transmission response fluctuations and assist in analyzing the location of the abnormality.
3. Identification and treatment of joint abnormalities of power and transmission
Sometimes power failures and transmission problems can have a cross impact, for example:
Compound Phenomenon | Linkage judgment |
Loss of power after a period of operation | Check if the generator is undercharged + electronic control module undervoltage protection |
Sudden stalling during gear shifting | Mostly electric clutch module signal disconnection / poor contact of the clutch switch |
Cannot move forward after braking sharply | Misalignment of the main drive shaft sheath or locking parts, it is recommended to re-disassemble and inspect |
No movement of operating handle / Instrument panel flashing | Mostly transmission electronic control module or shift potentiometer is damaged, it should be combined with the MINNUO diagnostic APP to read the fault code |
4. Preventive maintenance recommendations
Contents | Suggested periodicity | Inspection contents |
Check battery voltage frequently | Once a month | Voltage value should be more than 12.5V |
Change lubricating oil frequently | Every 500 hours | Main transmission oil, differential oil, clutch hydraulic oil |
Check clutch and generator belt tension frequently | Before each operation | Finger pressure should not sink more than 10mm, no slipping of pulleys |
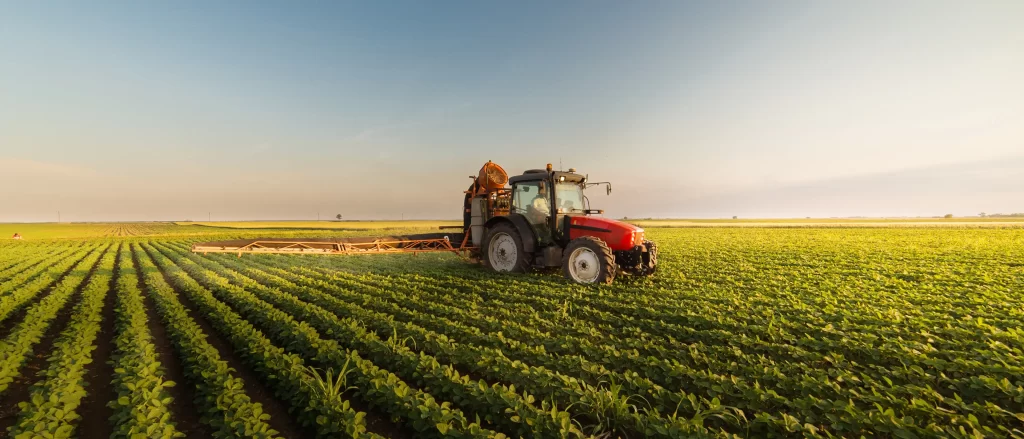
Ⅴ.The establishment of agricultural machinery failure warning and maintenance system
Modern agricultural machinery, high prices, complex structure, a single failure may lead to downtime losses of thousands of dollars or more. Therefore, the establishment of a scientific “predictive maintenance system” can significantly reduce maintenance costs, improve operational continuity and safety. The following are the three core components of the system:
1. Formulate a “phased inspection list”: set up maintenance nodes according to 100h, 500h and 1000h.
According to the operating hours of the equipment, set up different levels of maintenance cycles, and form a fixed inspection content.
Runtime node | Maintenance content (recommended) |
100h (initial warranty) | Change oil, oil filter, check battery voltage, tighten external screws, clean cooling grids |
500h (medium warranty) | Change fuel filter, hydraulic oil filter, check main drive shaft, gear lubrication, check drive belt tension and wear |
1000h (large warranty) | Check electronic control unit (ECU) parameters, actuator response speed, do a full body lubrication, clean sensors/filters, update software system |
✅ It is recommended to refer to the built-in maintenance cycle template in MINNUO intelligent equipment maintenance platform, combined with the automatic reminder of the user’s intensity of use.
2. Promote digital maintenance logs: Realize closed-loop management of equipment health records
Establish one machine and one file of “digital maintenance logs” to archive the use, maintenance, spare parts replacement and abnormal alarms of each piece of equipment, so as to facilitate traceability and predictive judgment.
Recording tools:
Use MINNUO APP or cloud console to automatically record “running time + fault reminder + maintenance completion status”;
support manual supplementary records, such as fuel consumption, replacement of filter elements and other records during non-networked operations;
export cycle report for technician’s reference, and can be used as an important evidence for applying for maintenance subsidies and warranty extension. The key fields include: start/end
The key fields include:
start/end time, running hours;
alarms and alarm codes;
maintenance items, part numbers used, maintenance person;
whether the inspection items are qualified (such as voltage, oil temperature, idling speed, etc.).
3. Introducing intelligent sensors + remote fault warning mechanism
The key to fault prevention lies in “detecting problems before they occur”. To this end, new agricultural platforms equipped with intelligent sensors and remote warning systems should be promoted.
Core functions:
Functional Modules | Detection content | Alarms |
Electrical System Monitoring Module | Battery voltage, current fluctuation, ECU response delay | App or SMS alerts are triggered when thresholds are exceeded |
Hydraulic System Monitoring Module | Real-time monitoring of line pressure, oil temperature change, abnormal oil pump load | Automatic generation of “Maintenance Recommendations” |
Engine Condition Monitoring Module | Abnormal rotation speed, high coolant temperature, abnormal injection parameters | Alarms and recommendations to “Reduce Load” or “Stop Work” |
Machine Load Analysis System | Compare the historical task intensity with the current pressure curve to determine the fatigue level | Early warning Early warning of “potential overload and wear risk”. |
Platform Recommendation:
MINNUO Intelligent Management Cloud Platform: Provides integrated functions of “fault code database + remote diagnosis + repair suggestion + technician docking”;
can be accessed by multiple devices, which is suitable for unified maintenance of family farms and cooperatives.
4. Suggestions and Precautions
Avoid sudden overhaul, and recommend the strategy of “365-hour small warranty + 720-hour medium warranty + 1,000-hour large warranty”;
Recommend the use of original standard parts for spare parts, and record the part number and time of replacement;
Recommend contacting the service personnel immediately if the fault code appears more than 2 times;
Guide the cooperatives to adopt the “Unified Maintenance + Sub-division Maintenance” strategy. Guide cooperatives to adopt the “unified maintenance + household use” model to reduce idle equipment and repeated purchases;
Guide farmers to participate in the online diagnosis course on the MINNUO platform to improve fault identification and judgment.
Conclusion
Agricultural equipment is the key guarantee for the efficient operation of agriculture, and the more it is used, the more it must not “fall off the chain” at critical farming times. Mastering the types of faults and troubleshooting techniques of common systems such as engine, hydraulic system, electronic control, power and transmission can help farmers quickly locate the problem in the first time, avoiding the equipment from being dragged into major repairs due to minor illnesses.
Proactive maintenance is far more cost-effective than after-the-fact repairs – through the establishment of regular checklists, digital maintenance logs and intelligent early warning mechanisms, farmers can not only extend the life of the equipment, reduce maintenance expenses, but also significantly improve the stability of the operation and the attendance rate of the farm machinery, so that in crop cultivation, the “long-lasting, stable, fast repair! In this way, the farm machinery can be used for a long time, stabilized and repaired quickly in crop cultivation.
As a representative of modern intelligent farm machinery platform, MINNUO is promoting the digital farm machinery management system integrating fault diagnosis, remote warning and intelligent control to help farmers realize the refined operation and maintenance mode of “predictable and easy to repair”, and build up an intelligent shield for the efficient operation of agricultural mechanization.