Currently, agriculture is facing multiple challenges: a persistent shortage of rural labor, increased instability of cultivation due to climate fluctuations, and increasing tension on arable land resources. Traditional agriculture’s crude input methods make it difficult to balance crop yield improvement and resource conservation, and there is an urgent need for a modernized management path that is “less manpower, high efficiency, and strong perception”.
The core concept of precision agriculture lies in “variable, quantitative, fixed-point, timed” optimization of each agricultural input, based on data support, on-demand management, maximizing the efficiency of resource allocation, so as to achieve high output per unit of land. It is not only a means to increase production, but also a fundamental path to realize green agriculture and sustainable development in the future.
In this transformation process, modern agricultural equipment plays a role in carrying on the role of the next. With the help of satellite remote sensing, soil sensors, self-driving tractors and other intelligent equipment, farmers can see the land like never before and make precise decisions. This article will focus on intelligent agricultural machinery systems, analyze how to land precision agriculture through technical means, and help readers build a set of practicable, scalable and efficient planting solutions.
Contents
- 1 I. Core Principles of Precision Agriculture and the Logic of Linking Agricultural and Mechanical Technologies
- 2 II. Interpretation of key agricultural machinery and equipment technologies to enhance crop yields
- 2.1 1. Intelligent irrigation systems: efficient valves for saving water and improving production
- 2.2 2. Soil Sensor System: Creating a “Data-based Soil Map”
- 2.3 3. Automated navigation and unmanned tractor: precise execution to ensure the quality of work
- 2.4 4. Multi-source data integration platform (platform-based management of agricultural machinery)
- 3 III. Practical operation path: four-step landing model of precision agriculture
- 4 V. Implementation Suggestions and Cautions
- 4.1 1. Investment Recommendations: Prioritize high-frequency processes and deploy them in phases to achieve the most cost-effective results.
- 4.2 2. Training and guidance: combining software and hardware, and bridging the last kilometer of “use it + use it well”
- 4.3 3. Recommendation for equipment compatibility: Choose a modular platform that is “upgradable + compatible”.
- 5 Conclusion
I. Core Principles of Precision Agriculture and the Logic of Linking Agricultural and Mechanical Technologies
The essence of precision agriculture lies in “decision-making with data” and realizing “differentiated management” and “automated execution” of agricultural activities. The essence of precision agriculture lies in “decision-making with data”. Through the synergistic linkage of intelligent farm equipment and data systems, precision agriculture upgrades the traditional experience of agriculture into a modern model that is digitally driven and prioritizes efficiency.
1. The Three Core Elements of Precision Agriculture
Data-driven
Key data such as crop growth, soil nutrients, moisture, and temperature are collected through satellite remote sensing, NDVI vegetation index, soil sensors, drone aerial surveys, and environmental monitoring stations.
The data forms a map of the field to assist in identifying planting needs and problems in different areas.
Variable-rate (Variable-rate)
Precisely divides plot management units (management zones) based on field data results.
Through variable-rate fertilizer application, variable-rate seeding, and quantitative spraying, it realizes localized and quantitative placement, and improves the input-output ratio.
Automation
With the help of driverless tractors, automatic navigation seeders, precision fertilizer application systems and other intelligent agricultural machines, it realizes automated operation after parameter presetting, significantly reducing human input and error rate.
Realize the change from “human command equipment” to “equipment independent decision-making and execution”.
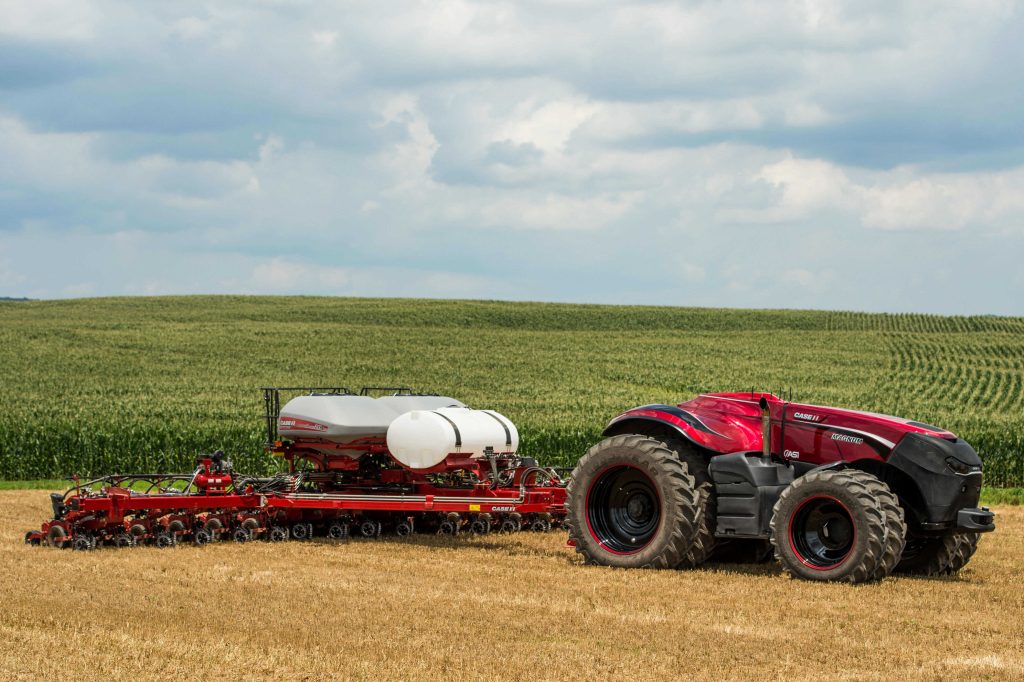
2.The three major technical roles of agricultural equipment in precision agriculture
Data acquisition terminal
Drone aerial survey: obtain high-resolution images of farmland to identify diseases, weeds, water distribution, etc.
Sensor system: installed in the field or on the tractor, real-time monitoring of pH, EC, moisture, soil temperature, etc.
Remote sensing data sources: e.g. NDVI, EVI indices to assist in determining crop health status.
Intelligent Execution Equipment
Automatic Navigation Farming Machine: Utilizes RTK+GPS system to achieve ±2.5cm operation accuracy, reducing reseeding and omission.
Variable sprinkler irrigation equipment: Intelligently adjust the sprinkler irrigation volume according to the moisture difference in different areas.
Intelligent seeder/fertilizer applicator: automatically adjust seed or fertilizer delivery according to sensor feedback or data mapping.
Control decision-making system
RTK navigation + farm operation map platform: realize path optimization, operation record, real-time tracking and other functions.
Farm management system (e.g., EMS or FarmOS platform): for integrating multi-source data, outputting variable operation schemes, and scheduling automatic farm machines for execution.
3.The additive effect of modularized farm machinery
Precision agriculture not only relies on “smart”, but also needs “variable”, and modularized farm machinery is naturally adapted to the demand for precision management.
Different modules can be deployed according to “variable blocks” (e.g. variable spraying arm, seeder with GPS).
Modules can be quickly replaced, realizing cross-season, cross-crop and cross-region operation demand response.
In the future, AI algorithms and remote sensing systems will be deeply integrated to realize module identification + adaptive parameter regulation.
4. Practical Summary
Elements of Precision Agriculture | Technical support | Expected results |
Data Driven | Soil/weather sensors, UAV image analysis | Realization of field variance identification |
Variance Management | Variable sprinkler irrigation, variable seeding modules | Input savings of 10-30%, yield increase of 5-15% |
Automated Execution | RTK driverless tractors, automated seeders | Operational accuracy >95%, labor savings |
II. Interpretation of key agricultural machinery and equipment technologies to enhance crop yields
The goal of precision agriculture is not only to “plant accurately”, but also to “plant well, manage carefully and harvest more”. Under the guidance of this concept, agricultural machinery and equipment are upgraded from “execution tools” to “intelligent housekeepers”, and play four core roles in the full-cycle management of crops:
1. Intelligent irrigation systems: efficient valves for saving water and improving production
Technical key points: Pressure control + GPS spot identification + crop water demand modeling linkage Identification + Crop Water Demand Model Linkage
Application Scenarios: Field Planting, Orchard Drip Irrigation, Facility Agriculture Sprinkler System
✅ Yield Boosting Mechanisms:
Reduce the crop stress response brought about by water-scarce areas and over-irrigation
Control the rise of soil salinity, enhance root vigor and absorption capacity
Practical Tips:
Crop evapotranspiration modeling access to the irrigation system
Automatically adjust the length and frequency of irrigation in conjunction with the soil moisture sensors and weather forecast
Typical Cases:
A cooperative in Binzhou, Shandong Province used the intelligent drip irrigation platform to increase corn yield by 12% per mu and save 40% water at the same time.
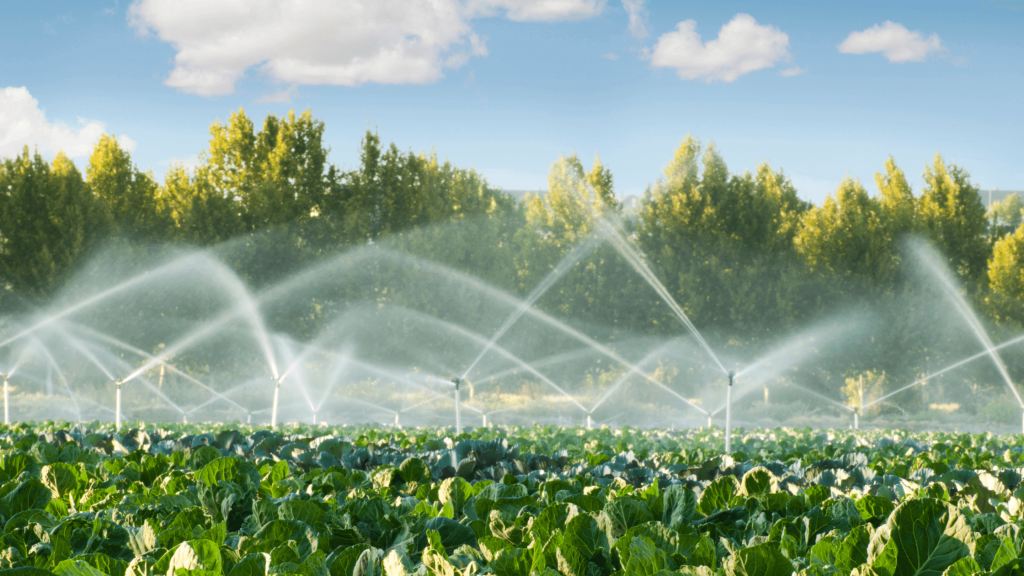
2. Soil Sensor System: Creating a “Data-based Soil Map”
Monitoring factors: pH, organic matter, water, salt, conductivity, temperature
Application value:
Distinguish between “strong and weak soils”, apply fertilizer in zones, and sow seeds in variables
Identify soil nodules, prevent and control diseases Source of outbreaks
Supporting equipment: variable fertilizer applicator, RTK navigation system
Operation suggestions:
Use the data platform to generate a “soil class layer” to guide the differential operation of machinery
Update the data once a season to dynamically adjust the crop rotation plan
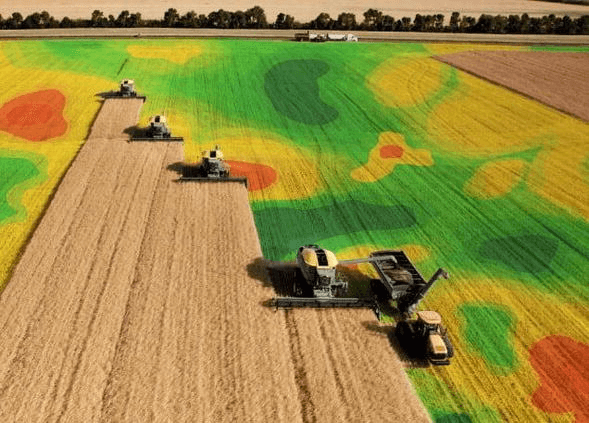
3. Automated navigation and unmanned tractor: precise execution to ensure the quality of work
Core technology: RTK differential Positioning ±2.5cm accuracy + road planning + tracking
Applicable operations: ploughing, sowing, spraying, fertilizing, harvesting
✅ Advantages:
Avoiding reseeding and omission, reducing the rate of re-cropping in plots
Precise route control, improving uniformity in row-plant spacing, and facilitating mechanization of harvesting
Difficulties:
First-time users need to familiarize themselves with the path planning software, and it is recommended to equip with smart terminals and touch screen devices
Not recommended for nighttime or heavily shaded areas Operation
Recommended equipment: MINNUO multifunctional navigation system, which can be synchronized with a variety of modular equipment
4. Multi-source data integration platform (platform-based management of agricultural machinery)
Role of the platform: Integrate operation records, soil data, meteorological information, planting track, etc., into a “unified management console for agricultural machinery.
Typical modules:
Intelligent sowing controller Controller
Spraying record system
Automatic identification module for variable fertilizer application
Electricity management (docking solar system)
✅ Practical value:
Unified scheduling of resources
Trace back the records of field management to help green certification
Precise grasp of “who, in which field, when, and with what machinery”
Case study:
MINNUO Intelligent Agricultural Machinery Platform Support Module Access + The MINNUO Smart Farming Platform supports module access and automatic data uploading, and has been popularized in Jiangsu, Hunan and other places, helping farmers to lose 15% weight per year and increase average mu yield by 8%.
Module Functions | Yield Improvement Principles | Adapted agronomic links |
Smart Irrigation System | Reduce water stress, improve root uptake | Post-planting to tasseling |
Soil Sensing System | Customized fertilization program, reduce waste | Pre-planting soil management |
Driverless Agricultural Machines | Improve seeding/spraying/fertilizing accuracy | Full operational cycle |
Agricultural Machine Data Platforms | Unified Management + Improve Operational Decision Accuracy | Full operational cycle |
III. Practical operation path: four-step landing model of precision agriculture
The essence of precision agriculture is “data-driven optimization of agricultural decision-making”. The implementation path can be divided into four stages, from “data perception” to “digital closed loop”, and each step can be completed by modern agricultural equipment and platform systems.
Step 1: Establish a basic database of the field
Goal: To find out the bottom of the plot and realize the “digital base map” for fine management
Action content:
Use soil sensors, plant protection drones, and multi-spectral remote sensing imagery to collect information on pH value, organic matter, moisture, and hot spots of diseases and pests.
Introduce NDVI/warm, humid, and light data, and analyze the differences between the growth of the crop and the field. Analyze crop growth and field differences.
Recommended equipment:
Soil integrated monitoring station
Drone + remote sensing terminal (with NDVI sensor)
MINNUO agricultural terminal system interface with telemetry data
✅ Practical suggestions: It is recommended to build a file at one time through a “whole-field census” or with the help of a third-party technical service, and then only need to update the local changes at a later stage.
Step 2: Precise Variable Zone Delineation and Formulation of Prescription Maps
Goal: Based on the differences of the plots, formulate precise instructions for fertilizer application, spraying, sowing and other operations.
Actions:
Generate a “Variation Layer” based on the Geographic Information System (GIS).
Call in yield maps, soil maps, and pest maps to form “Variable Prescription Maps. “
Combine with the weather platform to determine the variable strategy (e.g. delayed sowing in low-lying areas, multiple water applications in high-salt areas).
Recommended software platforms:
Variable management system + MINNUO intelligent agricultural data upload platform
Typical equipment linkage:
Variable fertilizer applicator, variable sowing equipment, strip spraying device
Application reminder: Precision agriculture does not necessarily cover the whole field, it is recommended to start from the topography of the obvious zoning plots. It is recommended to start with the obvious terrain zoning, and gradually expand.
Step 3: Deployment of automated operation
Goal: Realize precision farm machinery operation, reduce manual intervention, and guarantee standardized operation quality
Action content:
Use self-driving tractor with RTK positioning system to perform variable operation according to “prescription map”
Tractor automatically switches operation route/speed/intensity
Recommended equipment:
MINNUO Driverless module (supports ±2.5cm precision navigation)
Intelligent seeding controller + automatic variable spraying device
Data recording terminal uploaded to the management cloud platform
✅ Operational recommendations: first year can manually intervene in the trajectory to carry out the “assisted operation” mode, and in the second year to realize fully autonomous operation.
Step 4: Real-time monitoring and iterative optimization
Goal: Achieve “optimization while producing” and form a closed loop of seeding, management and harvesting data
Action content:
Simultaneously collect crop growth charts, spraying record charts, and sowing accuracy charts during the operation.
Automatically uploaded to the cloud-based agricultural platform, matching the behavioral trajectory of the operator and the quality of the operation scores.
Automatically generated “field performance report” at the end of the year. A “field performance report” is automatically generated at the end of the year to guide the adjustment of operation strategies in the coming year.
Recommended tools:
MINNUO Farming Machinery Management Cloud Platform
Digital Sensors + Intelligent Farming Equipment Terminal
Farmer’s cell phone Farming Machinery APP operation visualization interface
Practical tips:
Setting up a “field number” to track the operation of each plot for three years. The “field number” can be used to track the performance curve of each plot for three years.
It is recommended that farmers use crop fertility logs to form a full-cycle record that integrates hardware and software.
Comparison table between the four-step model and the function matrix of farm machinery and equipment.
Landing Stage | Technical Keywords | Representative equipment/platforms | Corresponding to agronomic objectives |
Step 1 Build library and map | data acquisition, sensing | Soil sensors, remote sensing drones, NDVI stations | Plot archiving, problem identification |
Step 2 Variable prescription | GIS, variable algorithms | GIS platforms, MINNUO Variable Configuration System | Differentiated management strategy development |
Step 3 Job deployment | auto-navigation, variable execution | Autonomous tractors, Variable Spraying Units | Improving operational accuracy and consistency |
Step 4 Closed-loop optimization | data return, map iteration | Agricultural cloud platforms, RTK management systems | Decision escalation, experience consolidation |
V. Implementation Suggestions and Cautions
The successful implementation of precision agriculture not only relies on technology, but also depends on the four-in-one synergistic mechanism of “reasonable investment rhythm + continuous training support + policy resource docking + equipment selection strategy”. The following is a list of specific recommendations:
1. Investment Recommendations: Prioritize high-frequency processes and deploy them in phases to achieve the most cost-effective results.
Recommended Path: Prioritize high input and high return operations, such as:
Irrigation: Install intelligent irrigation systems to solve the problem of “uneven irrigation and water and electricity consumption. Sowing: RTK navigation + precision sowing to improve seedling emergence rate and consistency
Spraying/fertilizing: Variable control system can reduce the waste of agricultural materials and improve the effect of pest control
Hands-on tips: Avoid one-time full set of inputs, and start from a field or single crop pilot, and then expand it year by year. 2.
2. Training and guidance: combining software and hardware, and bridging the last kilometer of “use it + use it well”
Suggested practices:
Sign a “remote technical support service agreement” with the supplier/dealer, and make regular visits + parameter optimization suggestions.
Organize farmers to learn how to operate the software platform, for example, job track export, variable prescription, and so on. Organize farmers to learn how to operate the software platform, such as exporting operation tracks, importing variable prescriptions, and checking the amount of fertilizer applied, etc.
Refer to the MINNUO Intelligent Agricultural Machinery Training Cloud Platform, and update the use of skills and case studies on a regular basis.
Extension plan: Jointly carry out the “Village-level Agricultural Machinery Operation Training Courses” with the local agricultural machinery schools and agricultural technology extension stations. 3.
3. Recommendation for equipment compatibility: Choose a modular platform that is “upgradable + compatible”.
After the Precision Agriculture System has been implemented, the possibility of “future upgrades” must be considered. Therefore, it is recommended that:
Recommended Configuration:
The mainframe supports quick module replacement (such as the MINNUO modular agricultural system)
Interface supports open communication protocol (compatible with different brands of variable spray nozzles/sensors)
Remote cloud platform can be accessed, which is convenient for accessing the carbon monitoring/subsidies docking system at a later stage
Extended Configuration Recommendation:
Motorized chassis + intelligent sowing module + cloud platform operation record system, which is an optimal combination at the initial stage. Program
If funds allow, prioritize the configuration of RTK positioning module to enhance the ability of precision control of the whole process.
Farm type | Starting Suggested Configuration | Upgrade direction |
Open field food crop farms | Smart Seeding + RTK Navigated Tractor | Variable spraying system, operation platform cloud upload |
Greenhouse vegetable farms | Smart Irrigation System + Data Acquisition Terminal | Light monitoring + air control module |
Joint family/cooperative farms | Motorized Tractor + Modular Operating System (MINNUO) | Multi-user data authorization system + time-sharing management function |
Conclusion
Precision agriculture is no longer the exclusive domain of large-scale agribusinesses, and it is gradually becoming an important means for small and medium-sized farms to improve yields, optimize management, and reduce inputs. With the support of data-driven, variable operation and automated control of key farm equipment, farmers can realize the “localized and on-demand operation”, effectively improve crop yields, save resources, and cope with the impact of uncertainties such as climate change on agricultural production. Especially in the context of fragmentation of arable land and diverse crop types, precision agriculture provides a real digital solution for growers of different sizes.
MINNUO, as a technology brand deeply engaged in intelligent agricultural equipment, is committed to integrating the trinity of “data collection + precise variable operation + intelligent scheduling and control” into its modular farm machinery platform, helping farmers build standardized and scalable intelligent farm machinery systems. Whether it’s precision seeding, variable fertilizer application, or visualization and remote management of operation trajectories, MINNUO can provide flexible, efficient and practical agricultural equipment solutions for farms of different sizes. The future of precision agriculture is starting with one intelligent farm machine.